The Dunnage Dilemma - Going Green with LEAN Sheet Metal Storage Racks
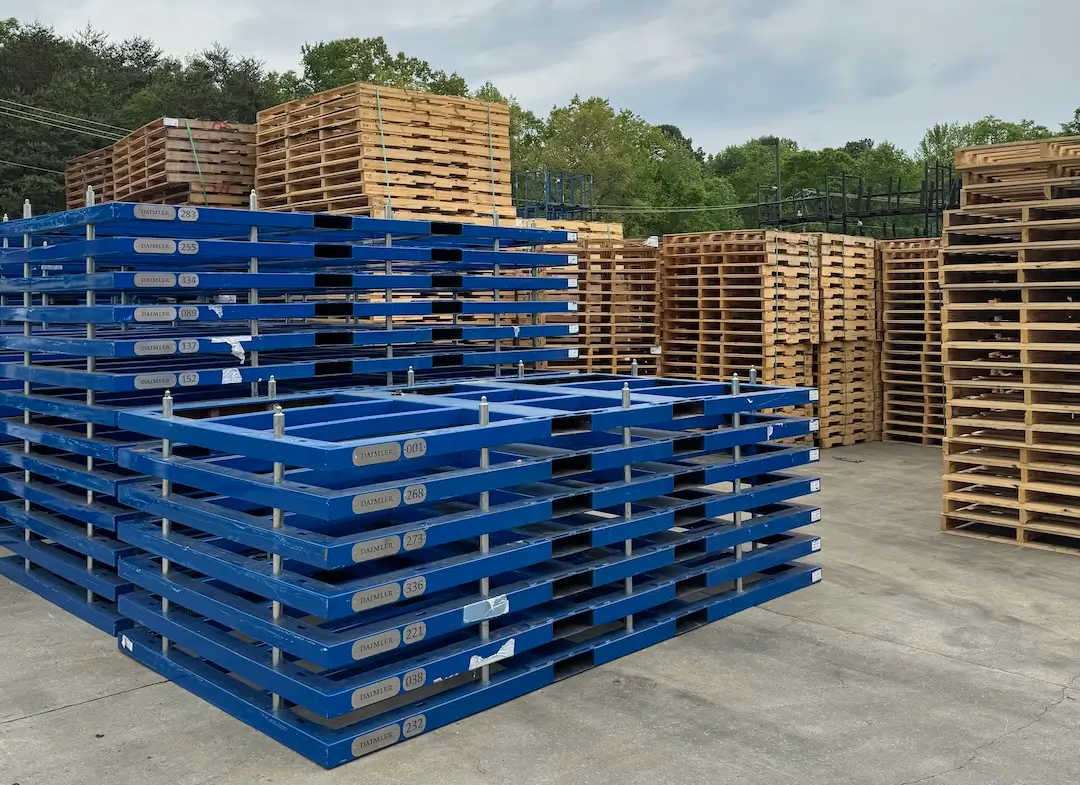
The History of sheet metal fabrication
Sheet metal fabrication has been a long-established process dating back to the 15th century when Leonardo da Vinci first sketched his idea for a rolling mill. It was not until the 16th century when reports of two rolling mills were designed: one to obtain gold sheets with uniform thickness and the other to cut already formed sheets into strips. The very subtle sheets were then used to make jewels, and further fabricated into shields or armor parts. It wasn’t until the 17th century when liquifying cast iron into complex shapes came to light. Shortly after, the Industrial Revolution created a surge in demand for sheet metal work and was the catalyst for press brakes and assembly lines that increased the rate of production.
Today, sheet metal fabrication has accompanied the development of human civilization significantly. From automated production lines to robotic CNC press brakes allowing for more precise bends, sheet metal working continues to be refined. As more advancements in technology and infrastructure arise, the demand for sheet metal fabrication is exponential. Businesses are expanding their operations to keep up with the demand, but within the constraints of their existing facilities. For manufacturers all over the world, finding ways to operate more efficiently forces them to examine processes within that have not changed for decades.
Going green through the implementation of lean manufacturing is an effective alternative for companies to streamline their operations and display their environmental conscious initiatives within the capacity of their existing facility. With a vertically tiered, sheet metal storage system, LEAN Manufacturing Products achieves high efficiency for manufacturers. Our purpose is to keep the green light on for your production, reduce your environmental footprint, and save you money to sustain your business growth for years to come.
Disruptions within your supply chain
Unplanned downtime in production is one of the most hindering factors to a company’s overall revenue and growth. Stoppage in production is inevitable when there is no process to sustain the quality of the material that is running through the machinery. This is most prominent for sheet metal manufacturers who receive material on wood pallets.
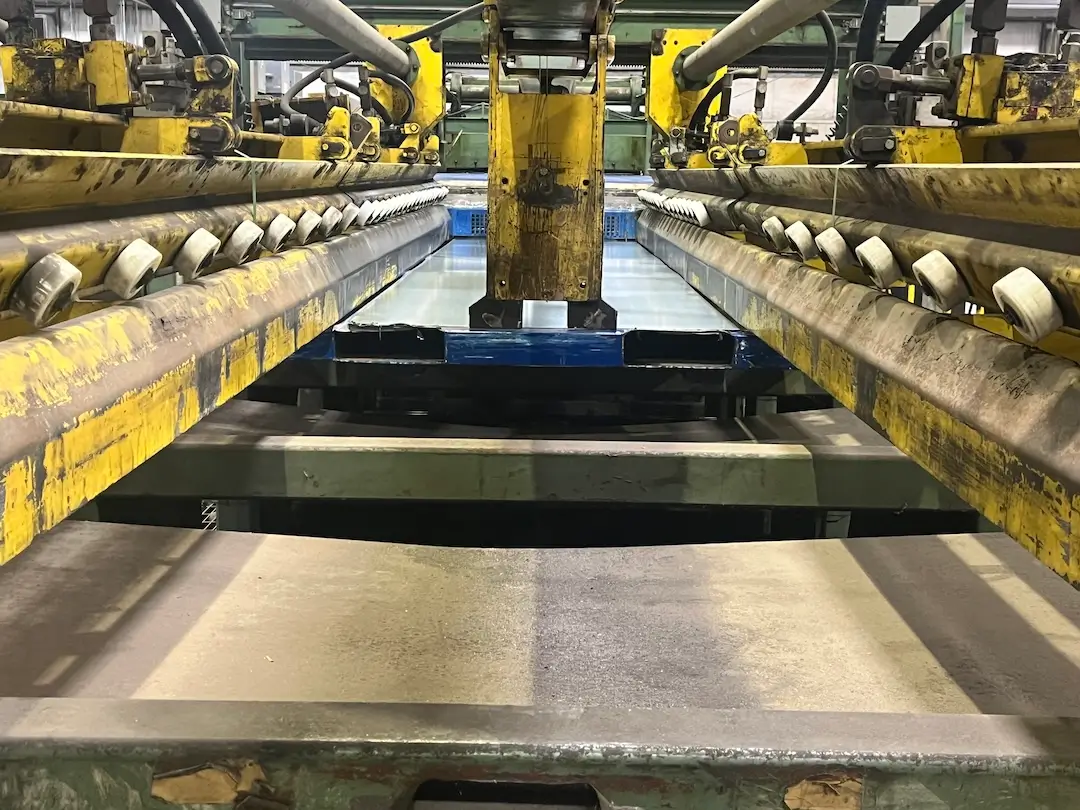
Although pallets are essential in transporting material, they can create disruptions on the shop floor. With sheet metal arriving on wood pallets, storing, and handling the pallets within the space allowed on the floor becomes a difficult task. With multiple touchpoints moving pallets around operators lose sight of where material is and how to get to it at a given time. While the green light for machinery needs to stay on, it becomes a burdening task when operators need to leave their work cell to find, unbury, and quality check their material to keep their machines fed. Using wood pallets in an automated system or production line can also become disruptive if the pallet fell or the quality was diminished after handling. Not only will that specific production line be stopped, but all lines downstream will be affected due to the bottleneck created by the wood pallet. Wasted motion to find material and stoppage in production directly affects the productivity of your business and delays shipments getting to your end customers. Disruptions to production are inevitable but can be mitigated by integrating the right solutions to sustain your operations and productivity on the shop floor.
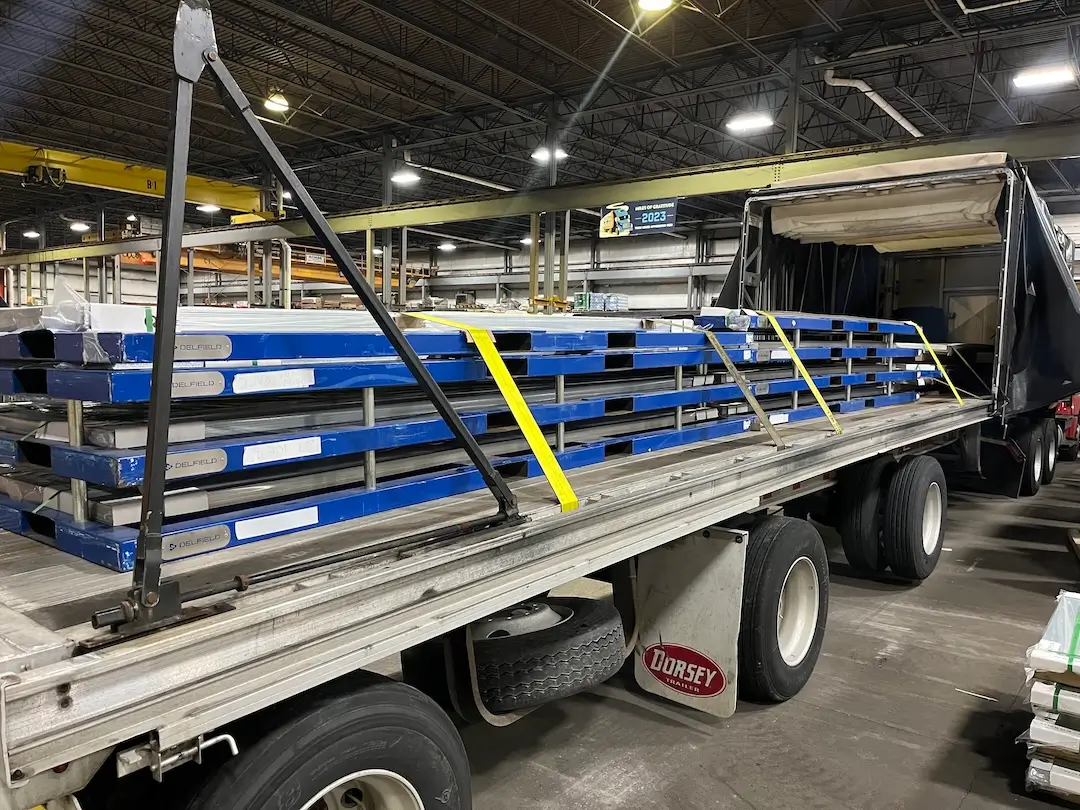
Material dunnage and the environmental impacts
Proper material packaging is often an unforeseen investment that pays dividends on the shopfloor when the right materials arrive undamaged and can be easily transferable into production. The way material is packaged and braced during transit is often referred to as dunnage. While wood pallets are historically the most common form of dunnage for sheet metal manufacturers, it is not the most efficient, nor environmentally friendly way to move material.
Since 2001, steel consumption per capita has steadily increased from 150kg to 233kg in 2023. By 2050, steel production is expected to increase by more than 20% to sustain the continued rise of developments around the world. With more steel being processed than ever before, many do not see the environmental impacts and additional costs that wooden pallets carry with each load. The average lifespan of a sheet metal pallet is the transit time from supplier to vendor. Once the material is unloaded from the truck, the pallet becomes waste and any effort in moving the pallet is wasted effort. Returning or recycling pallets can be a short-term solution but are still attributed with additional costs to do so. Recycling pallets to a chip yard can be a sustainable practice of disposing of the pallets, however, someone will need to continuously oversee the process, expensing their time and energy to do so. As more sheet steel is processed, the never-ending cycle of finding ways to dispose of the pallets continues.
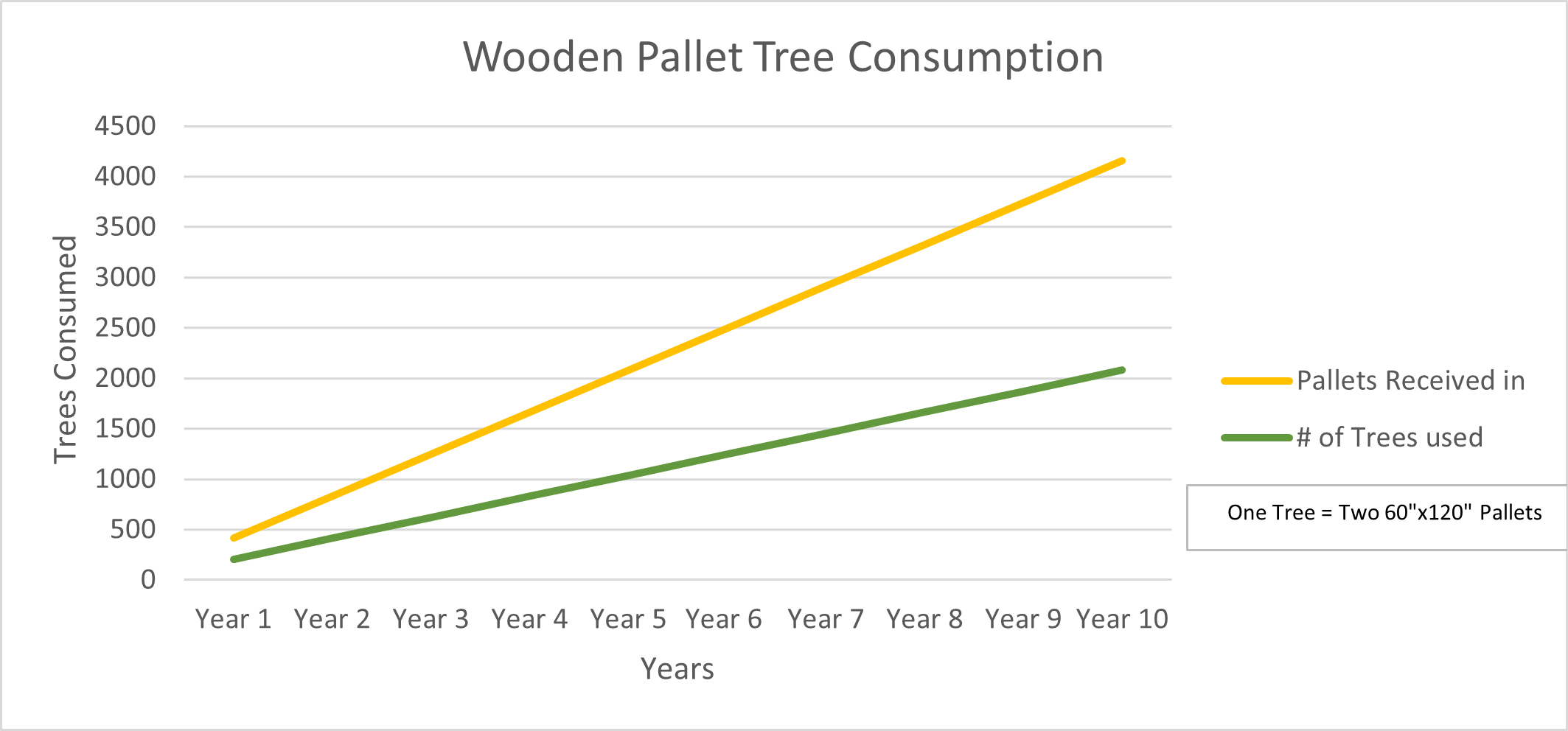
Let us take a deeper dive into what it takes to build a typical sheet metal pallet. On average, a tree can produce two 10’logs, which equates to roughly 63 board feet for each log. For a typical manufacturer, receiving up to 40,000 lbs. of 60x120 (50 BF) sheet material weekly equates to 208 trees per year if the material is shipped on eight pallets at 5,000 lbs. each. 208 trees may seem like a small number, but for manufacturers receiving shipments each week this number can become exponential as more steel is processed and received on a continual basis. A more holistic approach needs to be taken to see the true costs wood pallets carry with each load. Not only do they stretch the carbon footprint for manufacturers, but also accrue the costs of doing so onto their financial statement.
Financial analysis of sheet metal dunnage and handling
The way material is shipped and managed is far overlooked during the financial analysis for any business since it is assumed as a commodity to obtain their material. Although pallets may seem like commodities, they are recognized as true assets and come with a price. The expendable costs for wooden pallets in material pricing is not only an accessorial cost, but also accrues as more material is ordered and received. On average, the typical sheet metal wooden pallet costs $50-$100 each. With sheet metal received on multiple pallets on a weekly basis, that cost becomes substantial for any manufacturer.
Referencing the previous scenario, for a typical manufacturer receiving eight pallets of material each week that would account for roughly $800 per week or $41,600 annually of additional costs for wooden pallets alone. As material is received, material handlers have nowhere to store the pallets other than on top of each other.
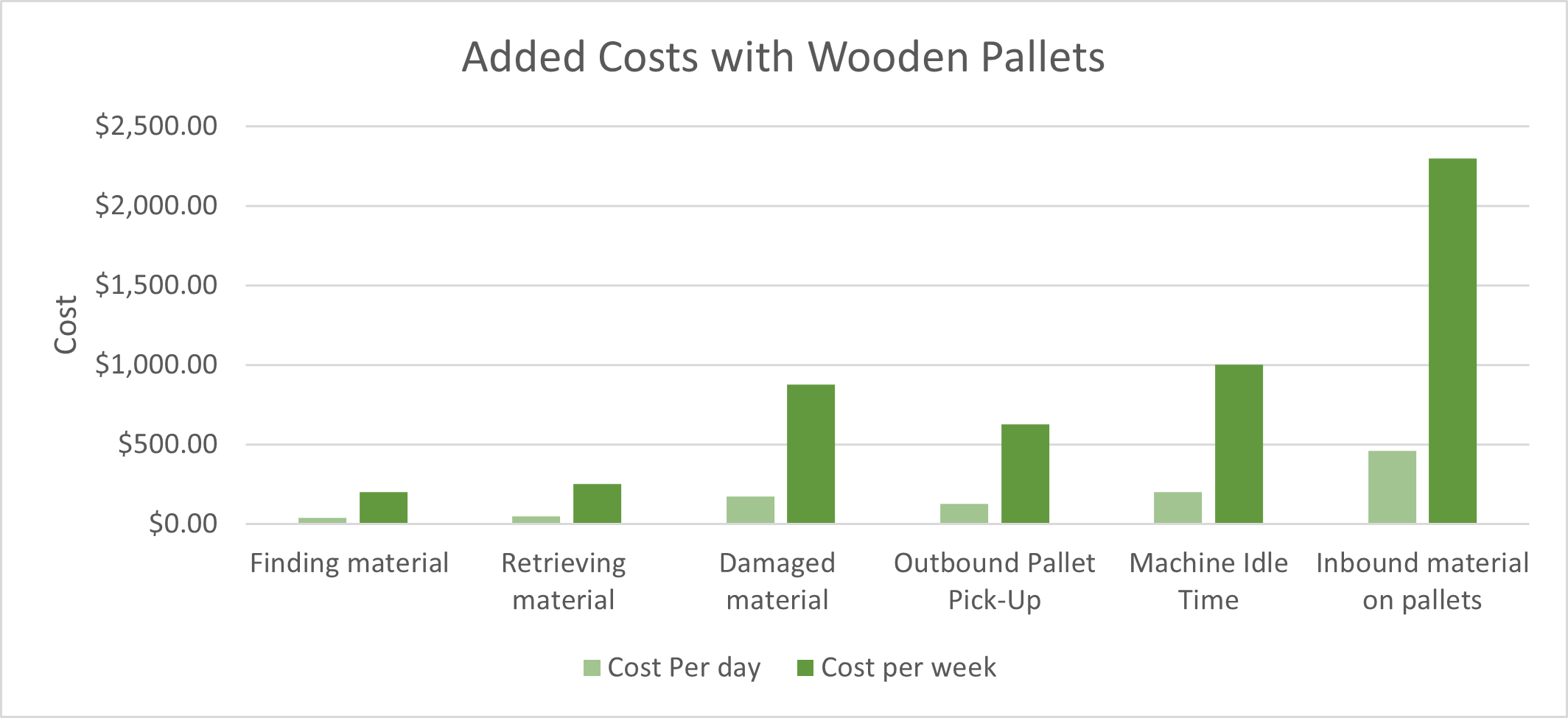
Although pallets may have a specific load rating when grounded, when placed on top of one another or in atypical cantilever style rack the pallet may not function according to the rating it was intended for. This is a widespread practice for sheet metal manufactures and can create serious safety concerns and substantial costs due to the added time it takes to move and obtain the material. Finding, retrieving, and checking that the material is not damaged are all non-value-added costs for a business. While operators are spending time looking for material, the machines that require the material begin to sit idle. The more idle time for machines the more production downtime for the business; directly affecting annual profit and lead times for the manufacturer. Taking a holistic view across the entire supply chain can lead to efficiencies that may have never been achievable and streamlined processes that have never changed for decades.
LEAN Manufacturing Products - Maximize efficiencies for your supply chain
LEAN developed an innovative solution to streamline sheet metal shipping and handling that creates cost savings throughout the entire supply chain for a business. With custom Re-Rack Sheet Metal Cartridges, material is securely housed within the cartridges, which are designed to optimize transportation to and from material suppliers. The utilization of these Sheet Metal Cartridges ensures that materials are well-protected during shipping and facilitates seamless operations. The cartridges can be stacked and engaged with one another, which evenly distributes the load capacity across the perimeter bushings without any additional weight directly on the material itself. By integrating Re-Rack cartridges into everyday operations, companies can enhance their material handling practices while reducing expenses associated with supply chain management.
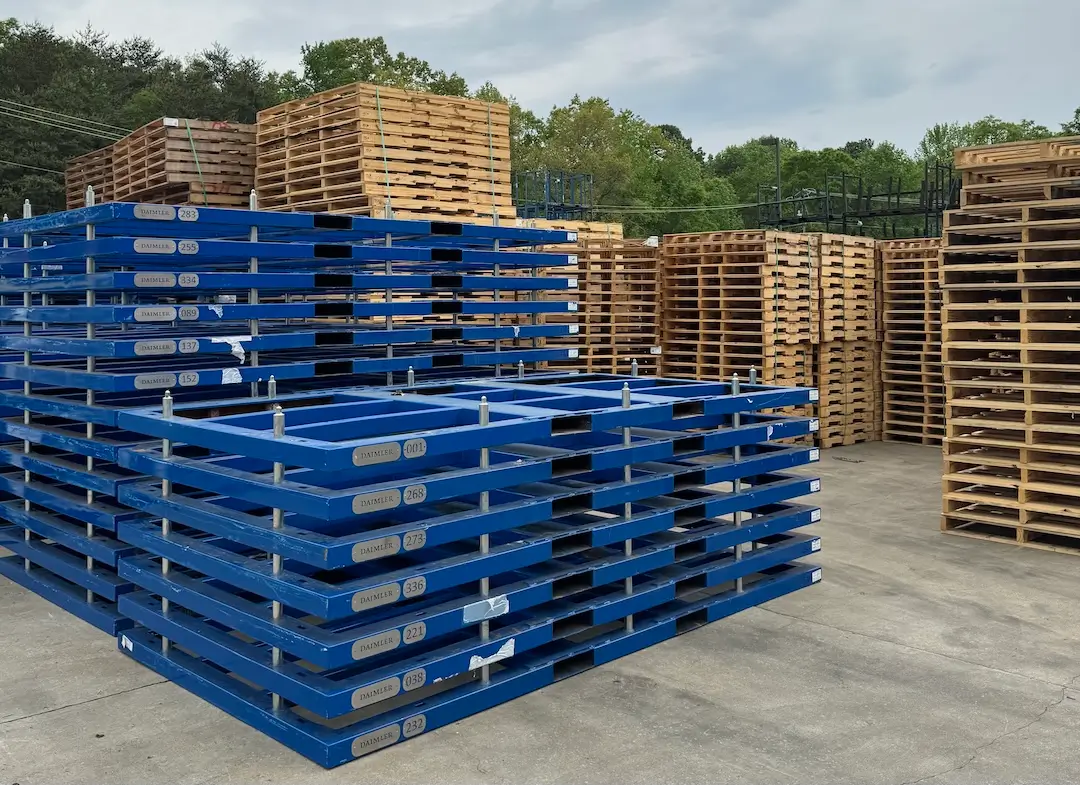
At a growing rate, Sheet metal suppliers and manufacturers are collaborating to enhance material delivery efficiency using LEAN re-rack cartridges. Integrating sheet metal re-rack cartridges into cut-to-length lines has streamlined material loading and shipment processes for both the supplier and manufacturer.
Steel Service Centers Incorporating LEAN in their Production Lines
Don Roddy, Operations Manager at Ryerson Steel, highlights the positive impact of LEAN cartridges in their operations, citing quality improvement, cost savings, and strengthened relationship between supplier and vendor.
“We spend less time building and refurbishing skids to get them back into production, and we have seen an increase in quality. When a material is on a wooden skid it is more susceptible to damage from the sides as well as on the top surface. With LEAN Re-rack cartridges it eliminates that susceptibility completely” stated Don.
Re-rack cartridges also facilitate a stronger relationship between vendor and supplier, creating a “milk run” process of sending and receiving sheet material. Establishing a safer protocol and guaranteeing the consistent delivery of high-quality materials to the vendor. “I would love to see the re-rack cartridges grow into a larger customer base and create more of a steady flow of shipping and receiving sheet metal” stated Don. “Ryerson embraces the green initiative through carbon tracking and by integrating LEAN cartridges we further limit our lumber use and reduce the concern for damaged material”. Ryerson's sustainability commitment is strengthened by employing carbon tracking and leveraging LEAN cartridges. This strategy not only cuts down on lumber usage, but also promotes an eco-friendlier operation. With increasing adoption of LEAN re-rack cartridges by suppliers in their production lines, the reliance on wooden pallets decreases, leading to a reduced carbon footprint for both the service center and manufacturer.
LEAN Sheet Metal Storage Systems Revolutionizing the industry
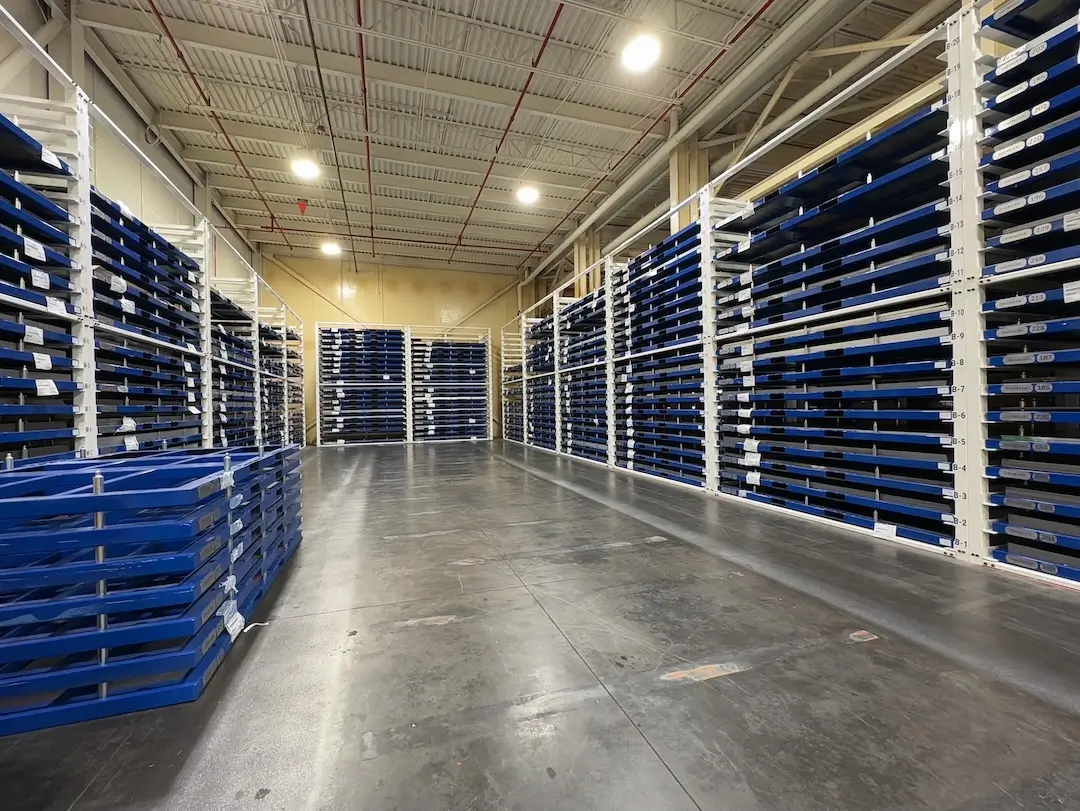
The use of LEAN Sheet Metal Storage Systems optimizes efficiencies for manufacturers throughout the supply chain. From material receipt, to staging, to machine loading; heavy-duty steel storage racking enhances these processes and integrating them into a manufacturer's operations can:
- Eliminate the concerns for damaged materials
- Save on fuel costs and on the number inbound material shipments
- Increase productivity by eliminating the need for operators to leave work cells
- Optimize machine utilization rates with less production downtime
- Streamline inventory cycle counting and material re-ordering
- Maximize floor space on the shop floor
Wood pallets represent an unavoidable cost for manufacturers, causing disruptions on the shop floor that impede company growth and sustainability efforts. By incorporating LEAN Storage Systems, sheet metal handling becomes streamlined, enabling a focus on value-added tasks to sustain production, lower environmental impact, and enhance overall business efficiency consistently.
Interested in investing in your own industrial sheet rack storage system(s) and/or metal material handling products?
View the LEAN Sheet Metal Storage Rack product page here > LEAN Sheet Metal Storage Racks
View the full LEAN Sheet Metal Storage Rack Image Gallery here > LEAN Sheet Metal Storage Rack Gallery
View our full product portfolio > LEAN Full Product Portfolio