Damaged to LEAN
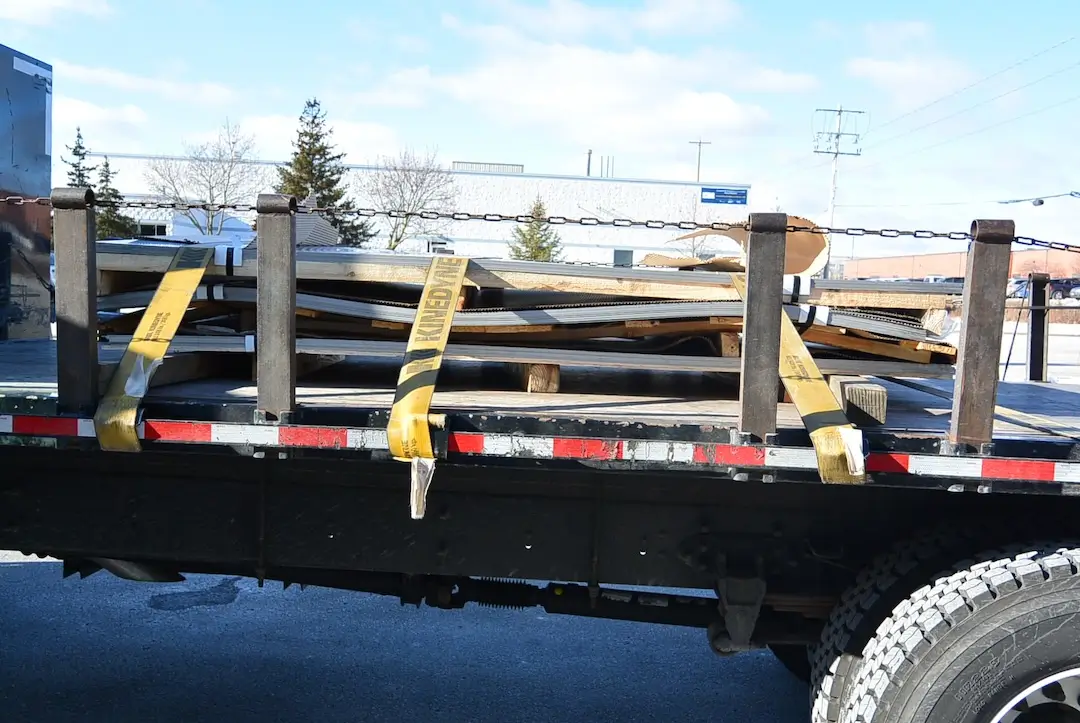
Procuring, Transporting, and Receiving Sheet Metal
The process of handling raw sheet stock typically begins at a sheet metal mill, where the material is coiled. From there, the sheet stock is transported by rail or truck to a service center.
At the service center, the material undergoes leveling, stretching, and shearing to meet customer specifications. Subsequently, it is re-handled and shipped to the end customer for offloading and inventorying. Once inventoried, the material proceeds through machinery for further fabrication in downstream operations.
Throughout the life cycle of sheet stock, multiple handling points exist, posing safety concerns for operators and vulnerability to material damage. Damaged material can significantly disrupt production, leading to increased machine downtime and additional expenses. Costs associated with managing damaged material include scrapping and incurring non-value-added expenses for the business.
Detecting damage during processing stages can be challenging, resulting in end customers receiving subpar material.

Sheet Metal Securement and Handling Risks
Sheet metal is commonly secured with banding and transported using wooden pallets, which might appear to be the industry norm. However, this method is extremely vulnerable to damage.
Storing large sheet metal on wooden pallets presents several challenges. Often, the only feasible option is to stack the material directly on top of each other. Unfortunately, this practice results in a cumulative load of thousands of pounds pressing down on each pallet. The material can become scratched, bent, and accumulate debris from the surrounding environment including moisture from the pallet itself, negatively impacting the material’s quality.
Fortunately, LEAN solutions exist to mitigate these risks and optimize the flow of sheet metal among all parties involved.
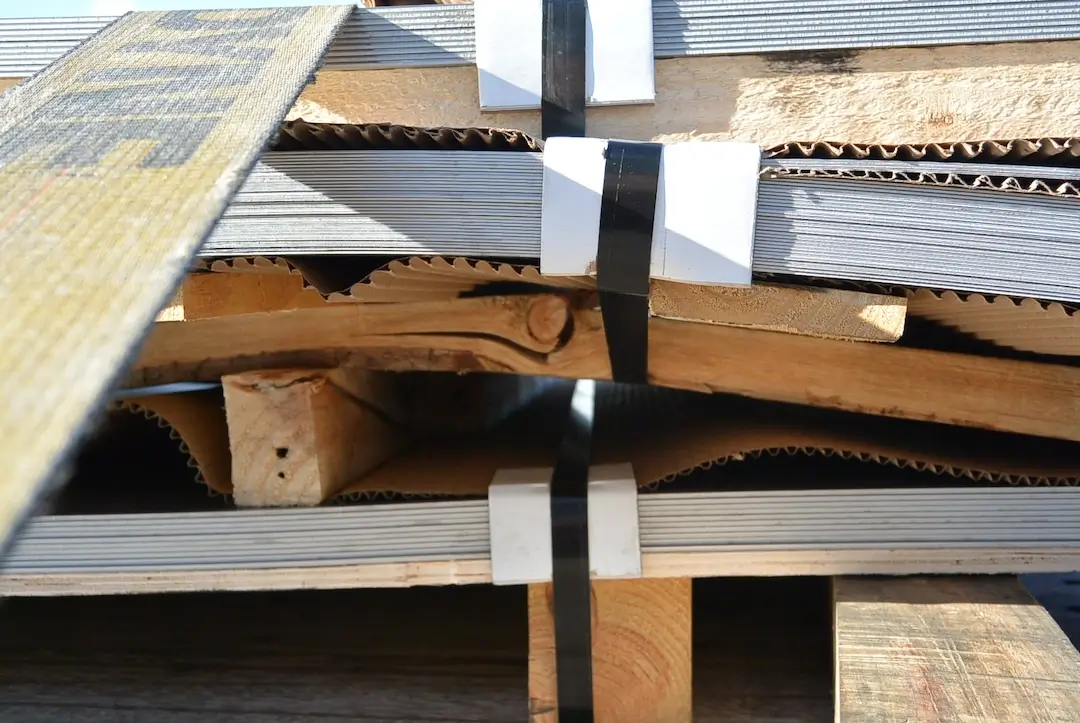
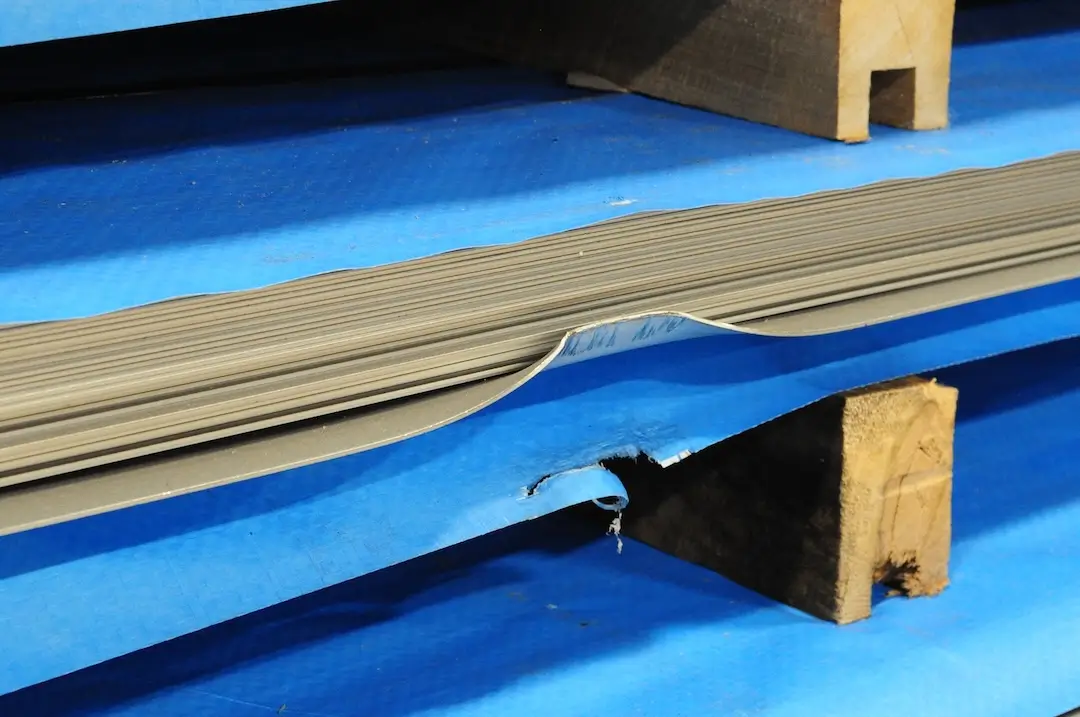
Safeguarding Sheet Material with LEAN Metal Storage Products
Our recommended solutions begin at the supply chain’s apex and progressively enhance processes at every downstream touchpoint.
Instead of haphazardly stacking material on inconsistently configured pallets, service centers can employ a more efficient approach by dropping metal directly onto LEAN re-rack steel cartridges. These cartridges are purpose-designed to ensure material quality with a streamlined flow and operator safety. When the material is prepared for shipping, they can be stacked uniformly, eliminating cumulative weight stress during transit.
Upon arrival at the manufacturer, the cartridges seamlessly transition into automation or into LEAN Steel Storage Shelves for staging, eliminating the inconvenience of stacking pallets directly on top of each other and optimizing material storage within a compact footprint.
Establishing a “milk-run” system for material transportation, LEAN’s reusable cartridges facilitate seamless logistics between fabricators and service centers, not only strengthening the relationship between both parties, but also ensuring an efficient process for replenishing inventory.
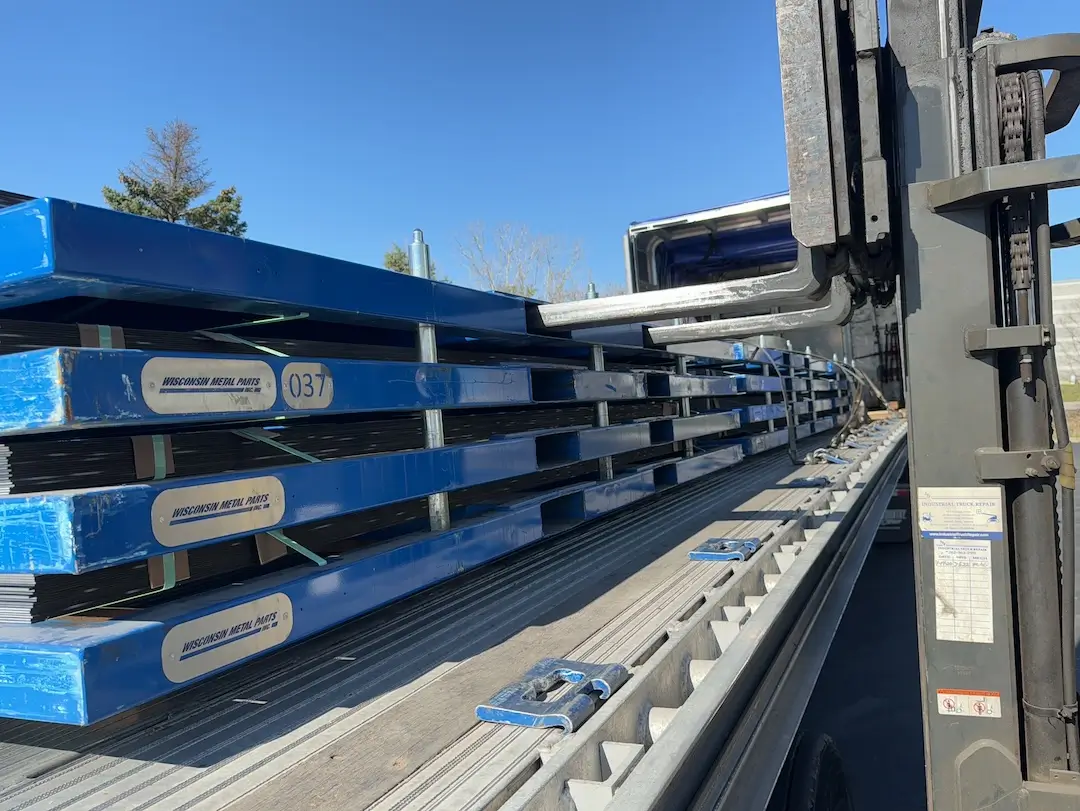
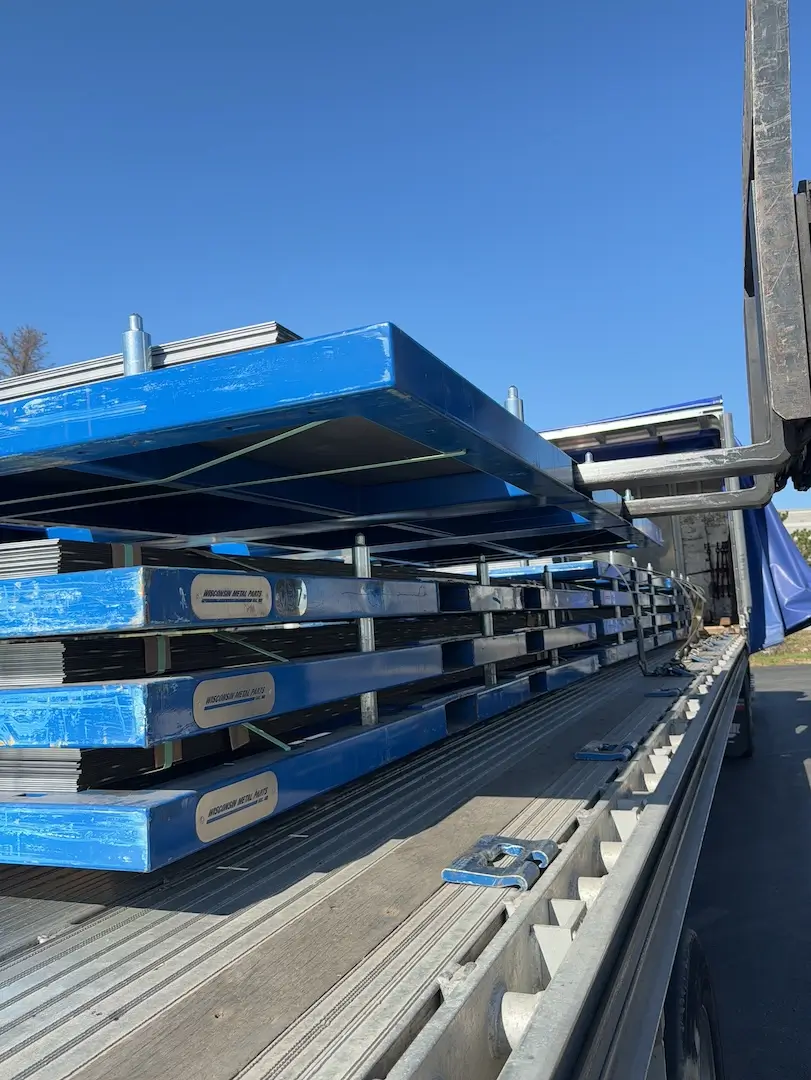
Need help with mitigating your damaged material challenges? Contact us today. Our team will help you to learn more about how LEAN Products can not only protect your metal, but also optimize your throughput, foster stronger ties between service centers and manufacturers, and pave the way for sustained growth in your facility.
View the LEAN Sheet Metal Storage Rack product page here > LEAN Sheet Metal Storage Racks
View the full LEAN Sheet Metal Storage Rack Image Gallery here > LEAN Sheet Metal Storage Rack Gallery
View our full product portfolio > LEAN Full Product Portfolio