The Path to Efficiency: Leaving Traditional Methods for LEAN Sheet Metal Storage Solutions
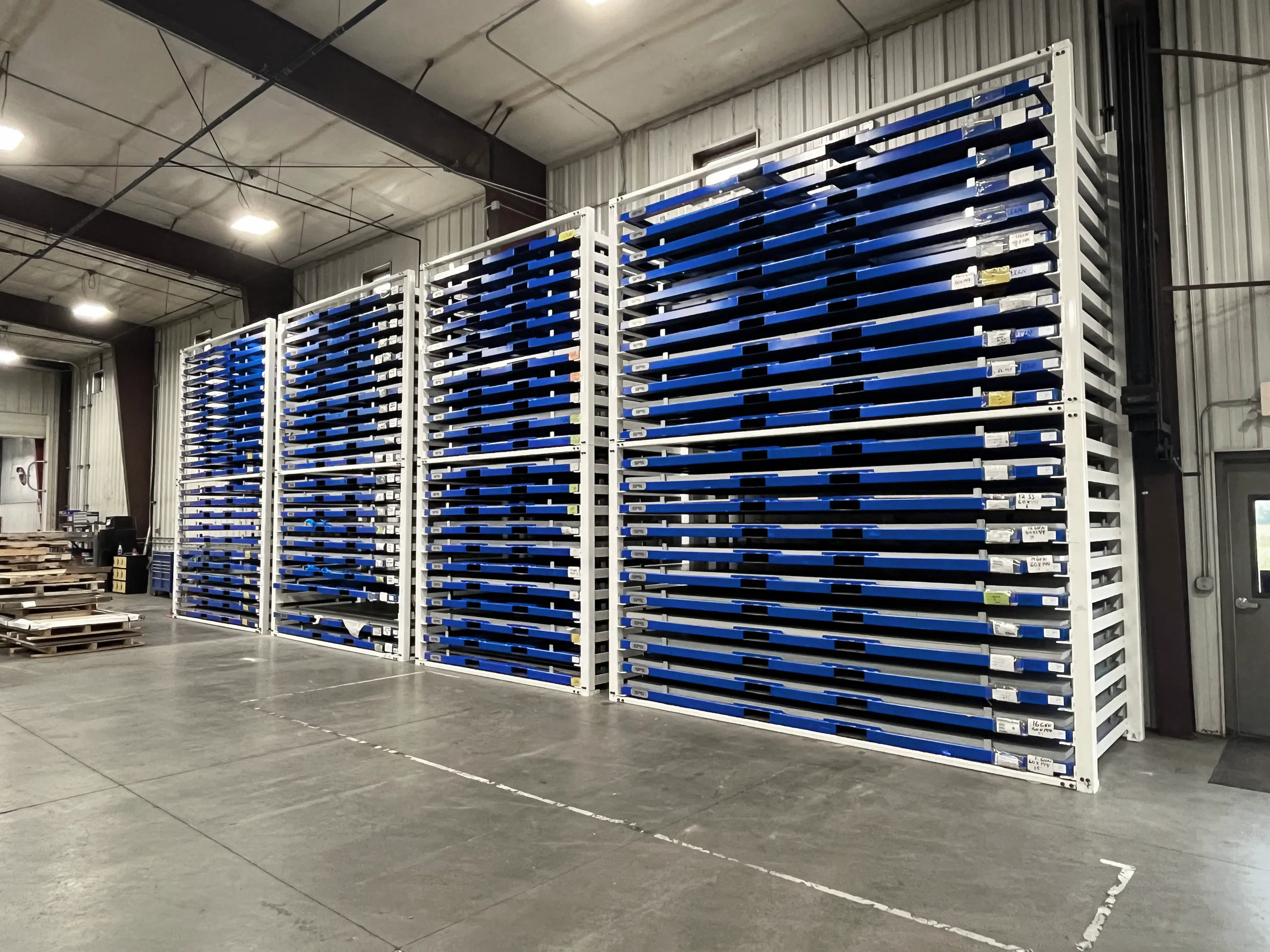
Managing the storage of raw materials that occupy significant space on the shop floor can be challenging, particularly when trying to maintain organization while meeting customer demand.
The ultimate objective is to achieve strategic and operational growth for the business, and this begins with optimizing the efficiency of your material storage.
Storing Sheet Metal
When managing sheet metal, storage typically begins with how the material initially enters the facility. Given the prevalence of wooden pallets in shipping and receiving, it's common for these pallets to be used for storage purposes as well.
While stacking pallets of sheet stock atop one another on the shop floor is a practice aimed at space consolidation, it often leads to inefficiencies in material retrieval and increases the risk of damage.
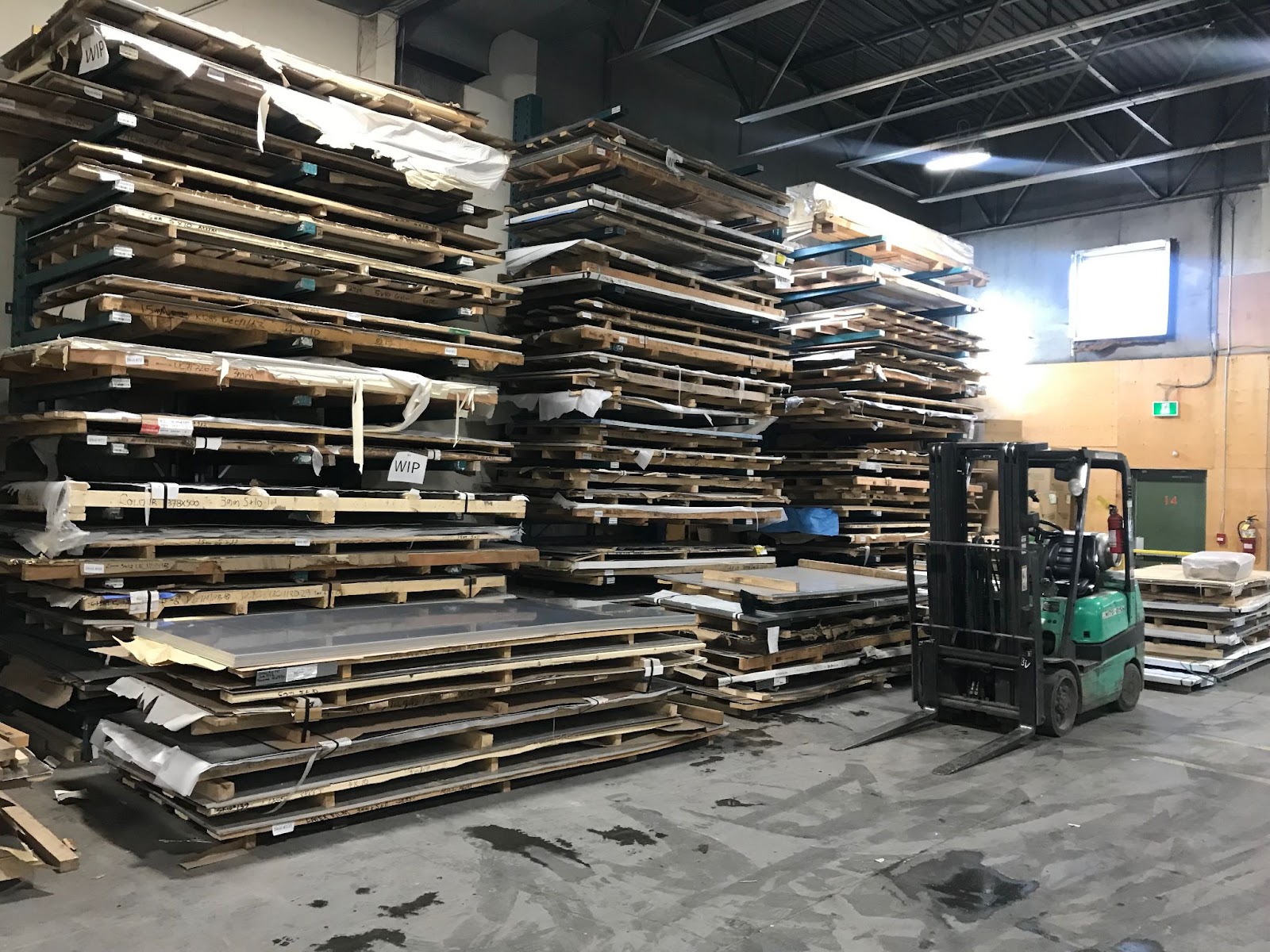
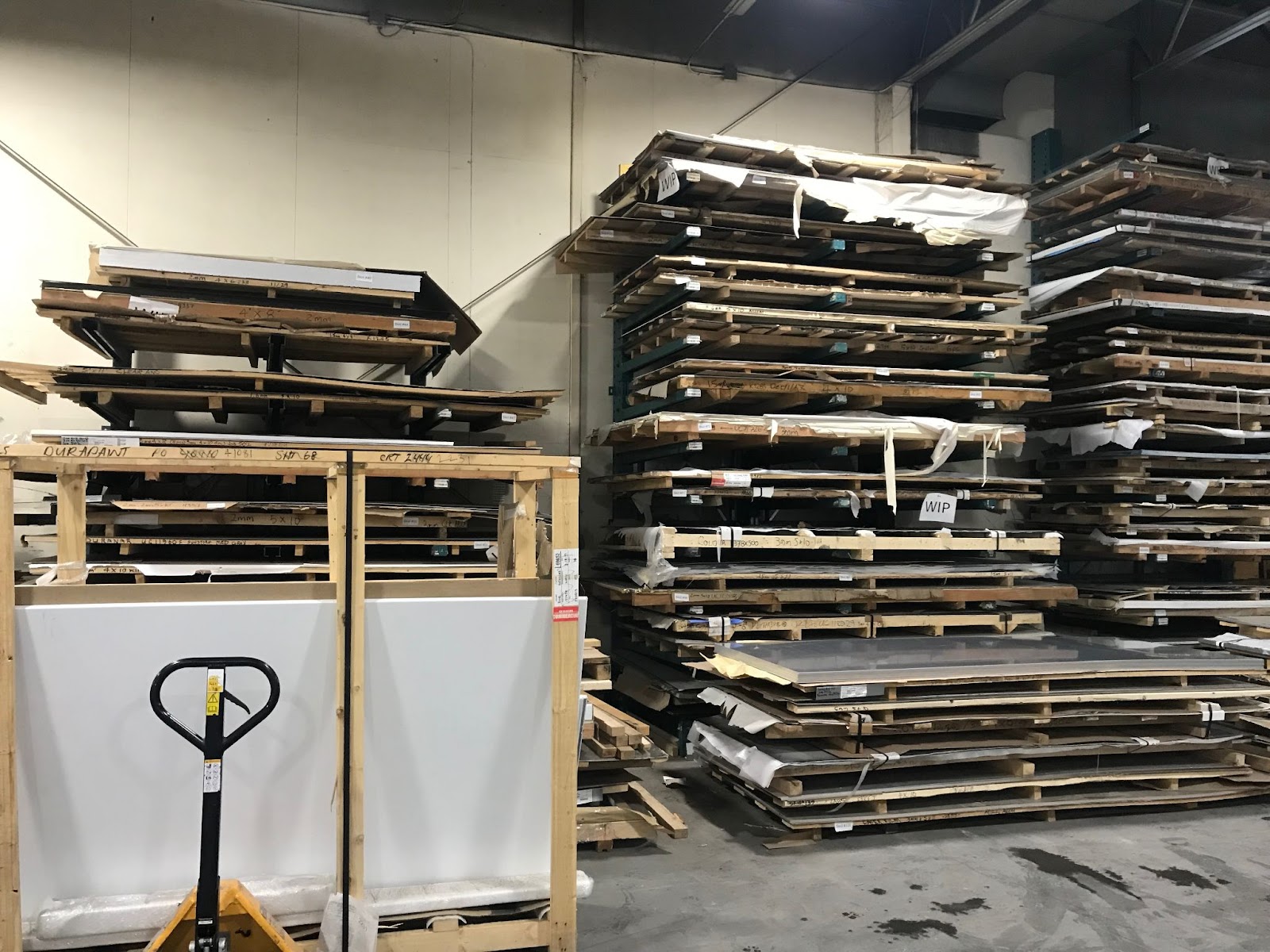
Traditional Material Racking Methods
Although sheet metal racking has been in use for some time, earlier designs were constrained by the traditional method of material reception. These designs lacked an efficient process for freeing material and storing sheet stock in a well-contained and easily accessible manner.
Several sheet metal racks are often perceived as "quick wins" for the industry, but ultimately prove to be more burdensome and time-consuming than beneficial. Examples of these include:
Rollout racks
Rollout racks are fixed and constrained to how far the shelving can extend. This design makes accessing materials more challenging and requires additional hoists, cranes, and or forklifts to free the material from the shelving unit it is contained in. Unless automated, rollout racks can also be labor intensive and time consuming, requiring operators to physically extend the shelving to retrieve the necessary materials.
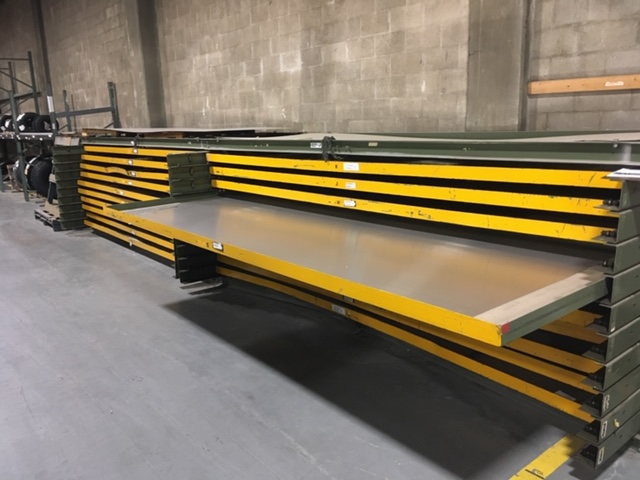
Cantilever racks
Cantilever racking is suitable for storing long items but may not optimize space usage for smaller-shaped materials. The design restricts accessibility, and the confined space within the racking can lead to wooden pallets being stacked atop one another, posing safety concerns, and resulting in inefficiencies when retrieving materials.
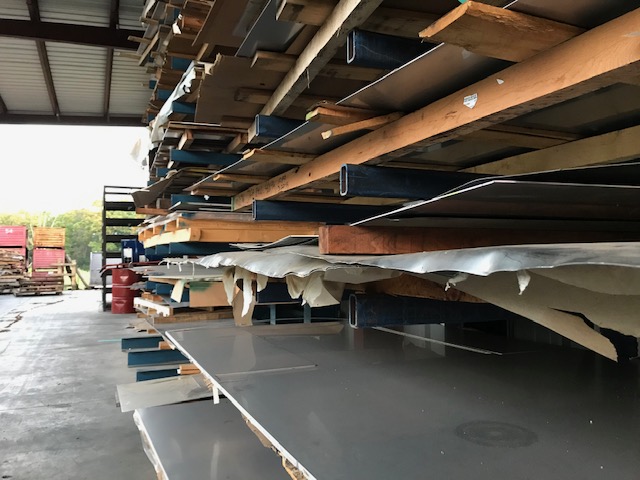
Automated storage towers
Automated storage towers come with a significant upfront investment. Due to the technology features integrated within the design, each feature drives the initial investment and installation cost. Given the intricacy of their design, these automated towers necessitate training and routine maintenance to ensure seamless automation functionality. In the event of mechanical failure, such disruptions can result in considerable downtime for all subsequent operations. Automated towers are limited in their storage capacity as well with a fixed number of shelving for material, which then requires offline storage to store the remaining inventory.
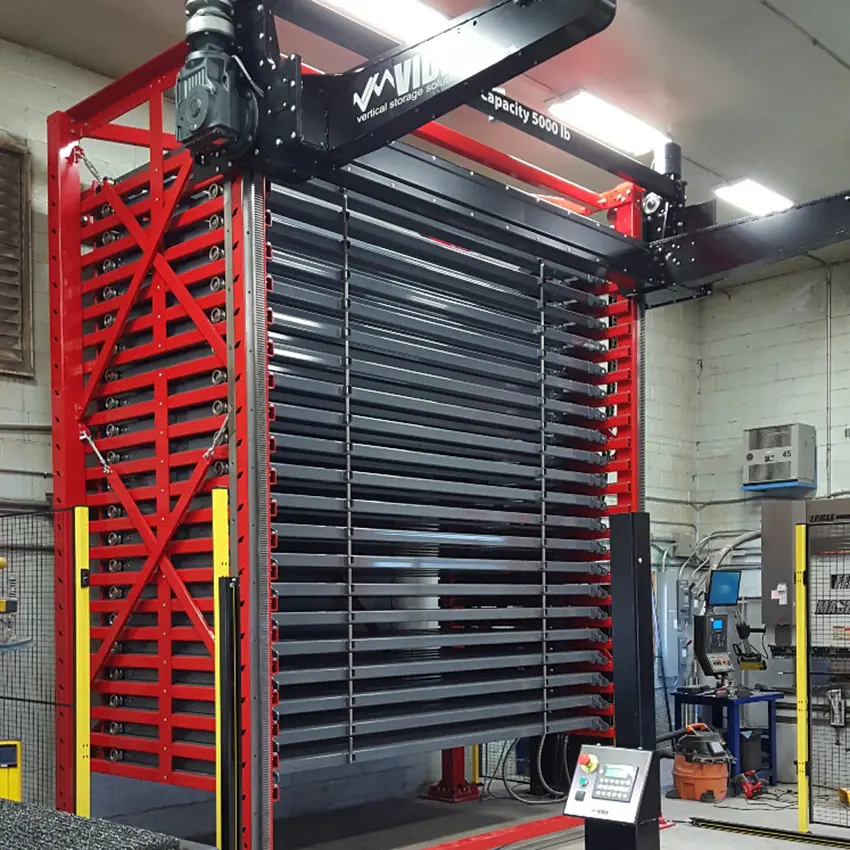
The initial investment into these alternative systems is not only substantial, but it is also important to consider the ongoing operational costs, including maintenance, upgrades, loss of productivity, and potential repairs each of these systems require over time. These costs can accrue and can significantly add to the total cost of ownership.
Points to Consider When Planning Out Your Operational Material Storage
When it comes to sheet metal or any other material storage in general, it is crucial to take several factors into account:
· Cost Effectiveness
· Size of your material
· Space constraints
· Accessibility
· Flexible and adaptable design
· Operator Safety
With intentional planning your operation will have the best chance to eliminate wasted space, movement, and time spent handling during each process.
LEAN Sheet Metal Storage
LEAN Sheet Metal Storage Racks are strategically designed to address these pain points.
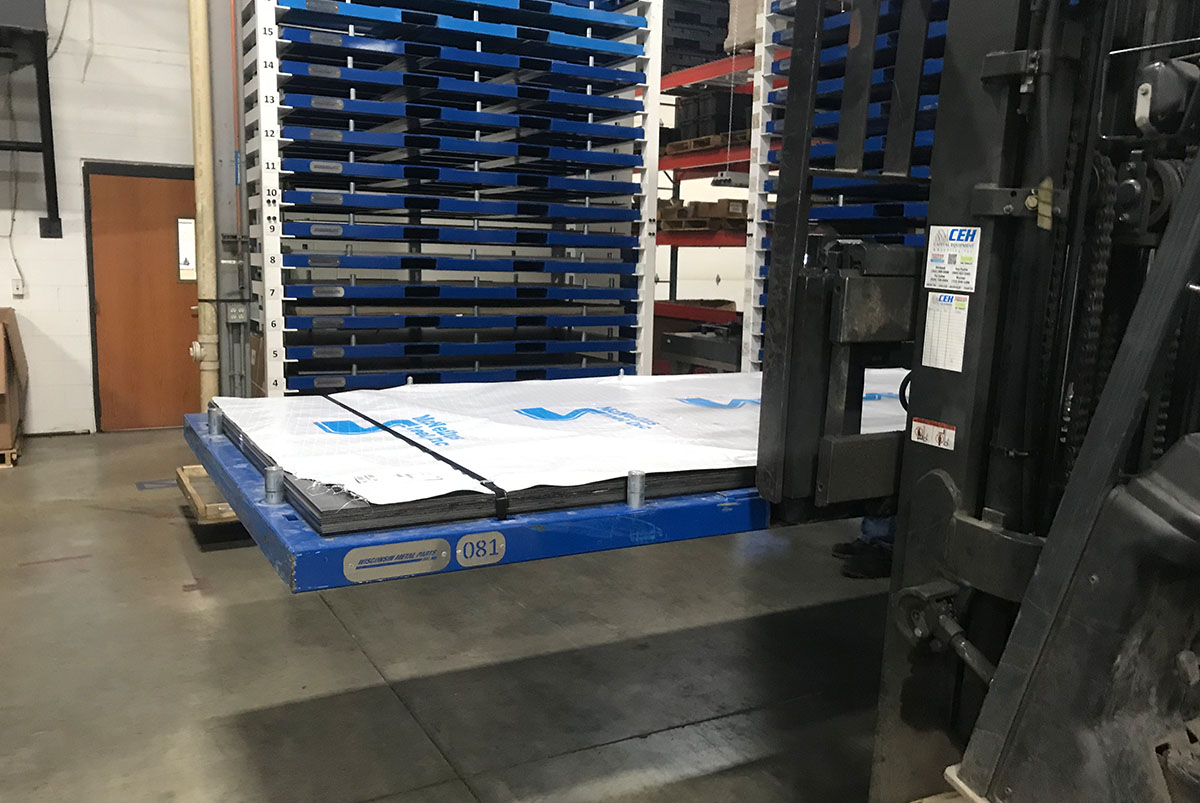
Every rack features multiple forklift accessible cartridges capable of holding up to 5,000 lbs. of material each and can be tailored to accommodate the dimensions of your sheet material. And with the adaptable and space-efficient design, they help optimize storage capacity, enabling you to store larger quantities of material within a minimal footprint on your manufacturing floor.
Equipped with perimeter features that securely enclose the sheet material within the cartridges, concerns regarding operator safety and material damage are also significantly reduced.
Our collaborative approach ensures that we find a solution to perfectly match your material storage needs and significantly streamline inventory management by consolidating materials into a vertically tiered cartridge-style racking system.
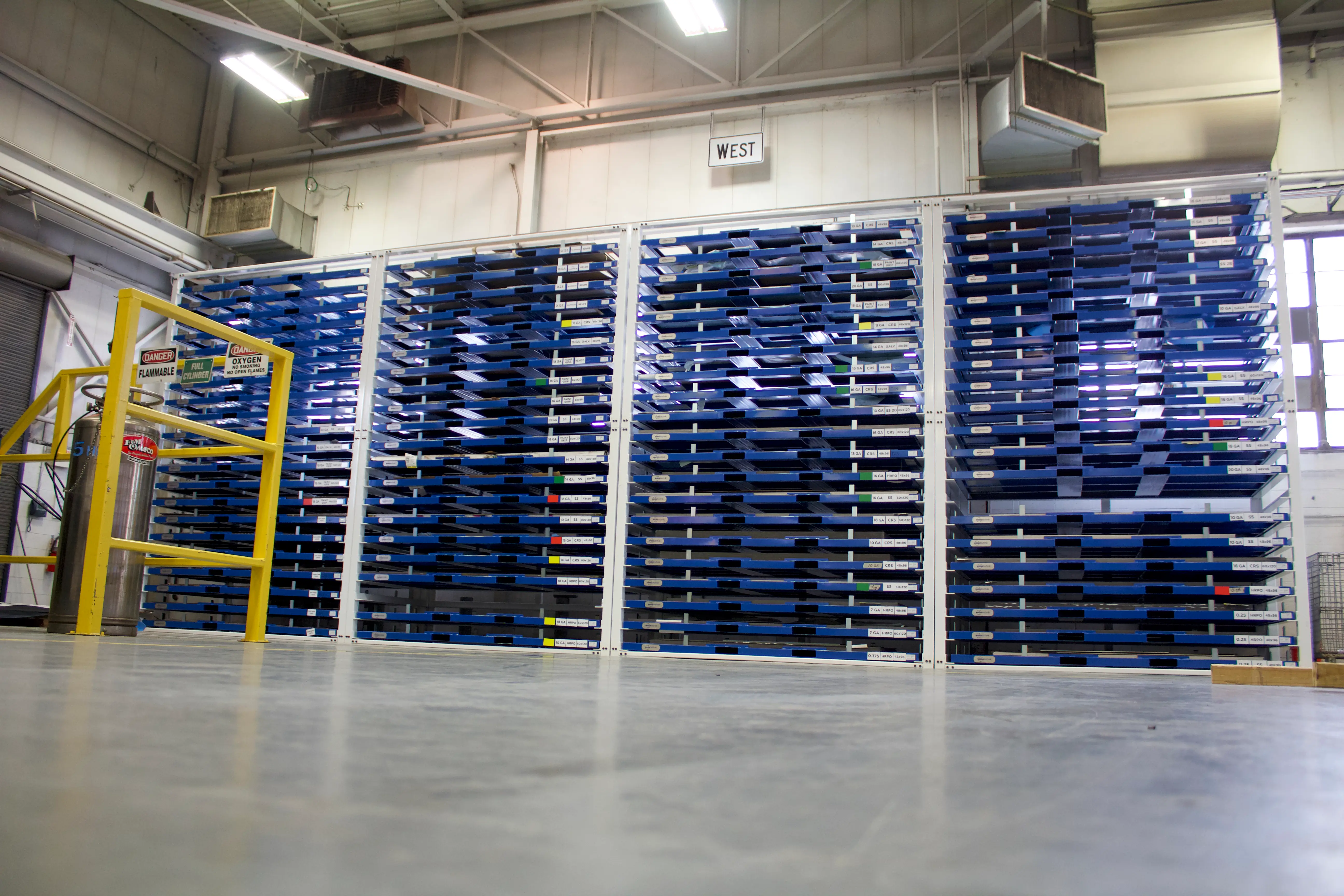
It's time to move beyond outdated practices and standard racking solutions for your material storage needs.
To see more about our Sheet Metal Storage Systems, visit the product page here.
Have questions? Give us a call at 262-875-3071 or shoot us an email at info@leanmfgproducts.com