What is Lean Manufacturing? Minimizing Waste in Your Operation
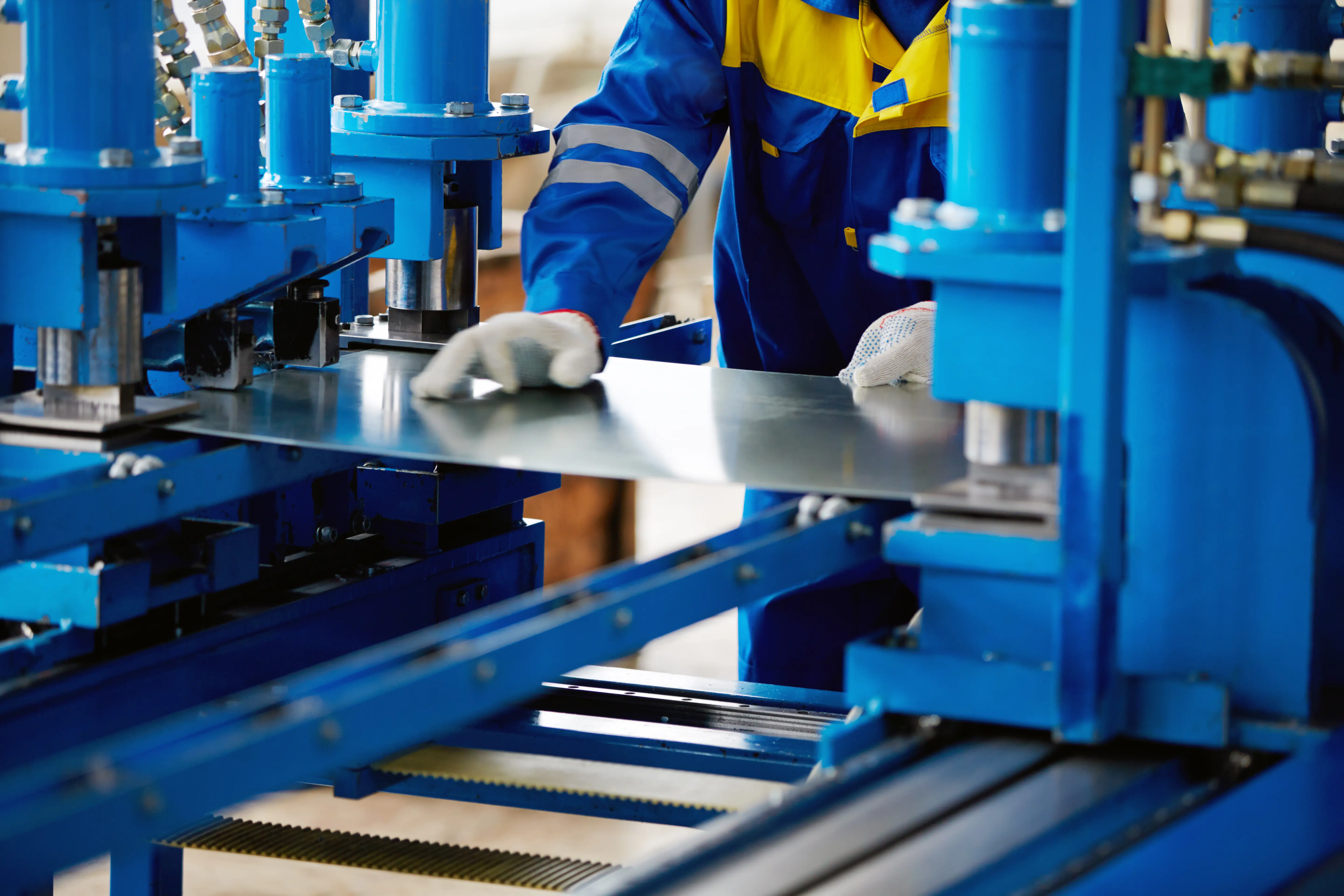
Lean manufacturing is a systematic method for minimizing waste within a manufacturing facility without sacrificing productivity. Simply put, it’s about creating room for value, not by making more, but by utilizing less.
The Origins of Lean Manufacturing
After the destruction of World War II, Japan was faced with severe resource shortages and economic challenges. In the midst of these challenges, automotive manufacturer Toyota was forced to find creative ways to do more with less.
Over the next 30 years, engineer and executive Taiichi Ohno, along with contributions from Eiji Toyoda formulated and implemented what is now known as the Toyota Production System (TPS).
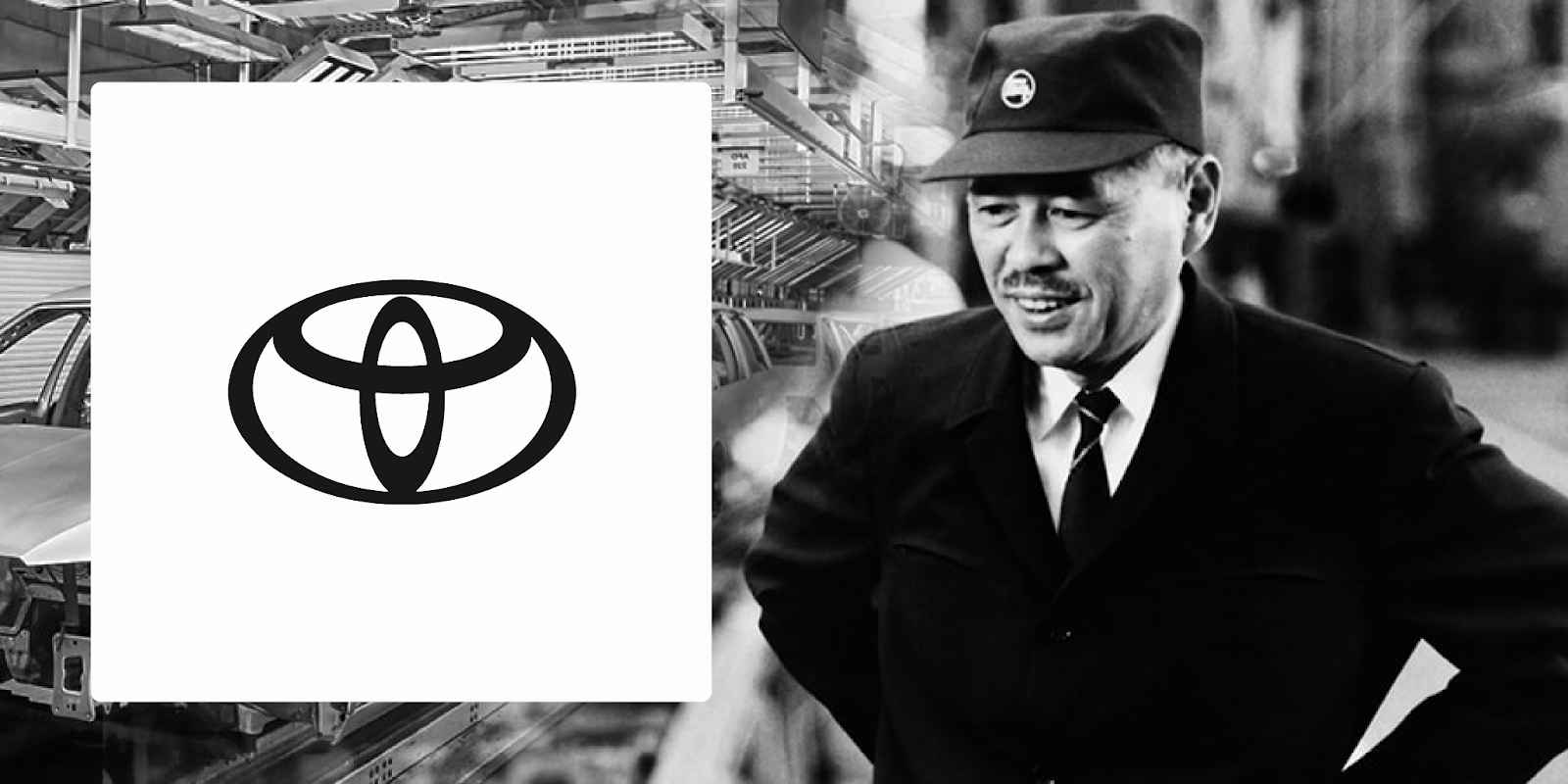
The methodology focuses on efficient production and elimination of waste to improve quality and reduce costs.
Key elements of the Toyota Production System include:
Just-In-Time: Producing only what is needed, when it is needed, and in the amount needed.
Jidoka: Automation with a human touch, which means stopping the process immediately when a problem occurs to prevent defects.
Kaizen: Continuous improvement involving everyone at all levels of the organization.
Heijunka: Leveling out the production schedule to minimize fluctuations and overburden.
Standardized Work: Establishing consistent methods and procedures for workers to follow.
Visual Management: Using visual cues to convey information quickly and clearly.
5S: Workplace organization method (Sort, Set in order, Shine, Standardize, Sustain).
TPS transformed Toyota and gave them the momentum to soon become one of the world's top automobile producers, reaching just over 3 million vehicles produced in the year 1979.
Heavily inspired by the methodology of TPS while studying at MIT, automotive business figure, John Krafcik, would coin the term "Lean" in his 1988 article “Triumph of the Lean Production System”.
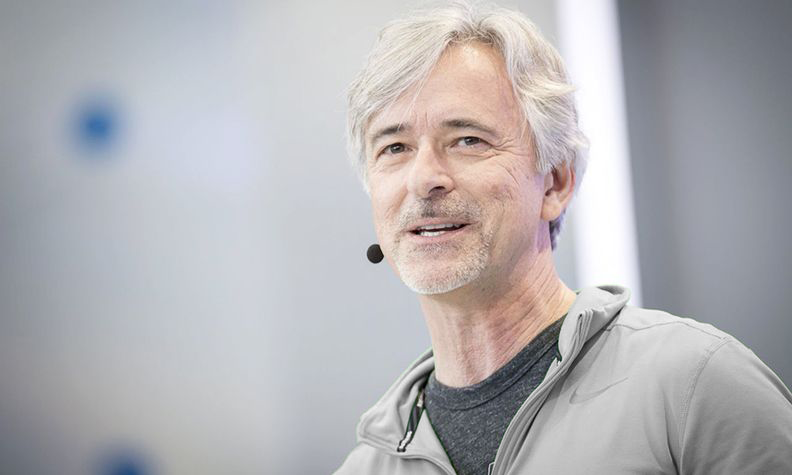
His work highlighted how these practices were superior in terms of quality, productivity, and flexibility compared to traditional mass production techniques and would spark a new wave of interest in the practice of workspace optimization.
So what exactly is Lean? The Five Core Principles
Lean manufacturing is built upon five key principles:
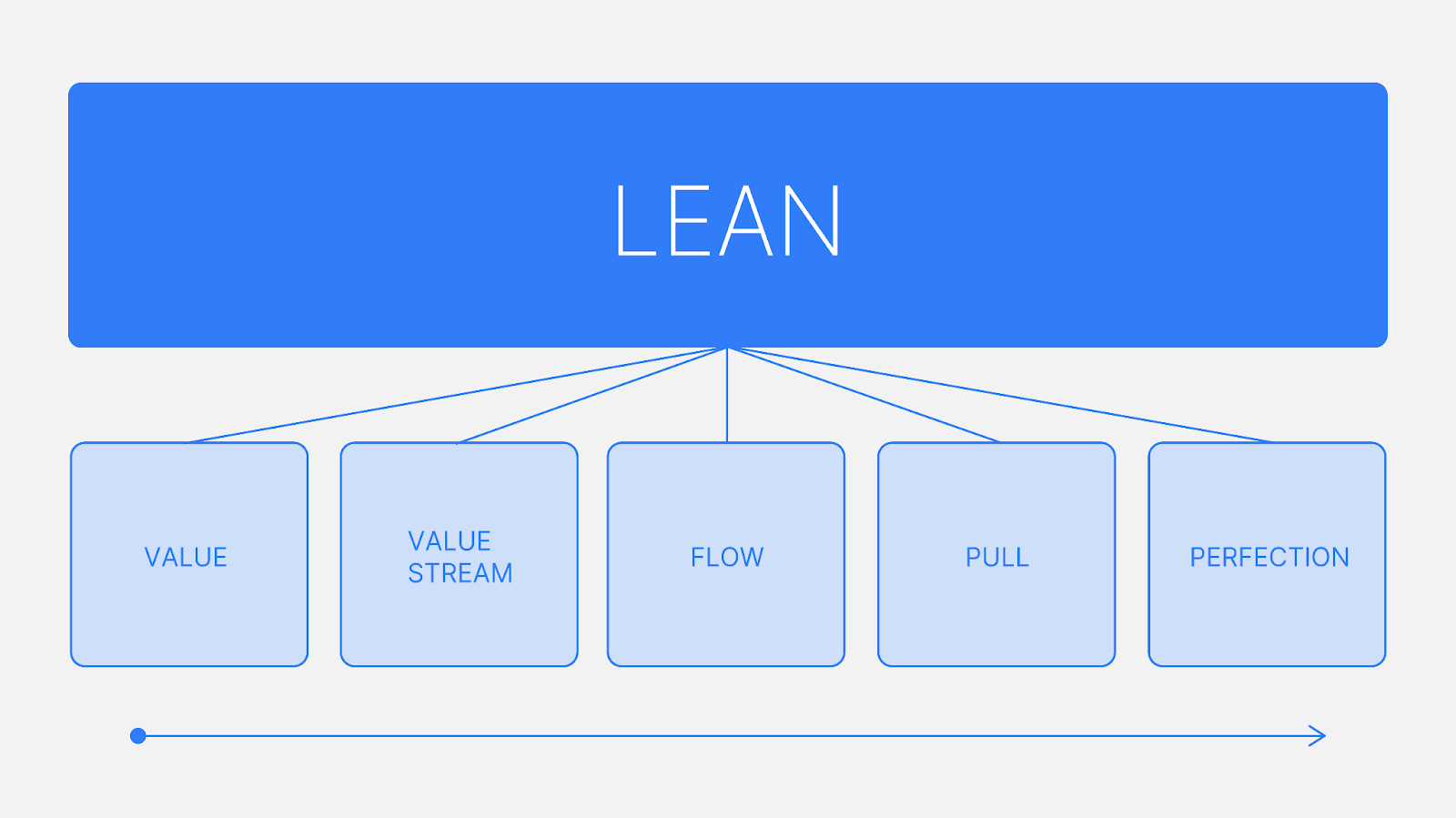
Value: Define value from the perspective of the customer. This means understanding what the customer needs and values in a product or service and ensuring that the company's processes are aligned to deliver that value.
Value Stream: Identify the value stream for each product or service, and map out all the steps in the process. This involves analyzing the entire flow of materials and information needed to bring a product from conception to delivery, and eliminating any steps that do not add value.
Flow: Create continuous flow by ensuring that value-creating steps occur in a smooth sequence without interruptions or delays. This principle focuses on streamlining operations to reduce lead times and enhance efficiency.
Pull: Establish a pull system where production is driven by actual customer demand rather than forecasts. This means producing only what is needed, when it is needed, and in the quantities required, thereby reducing excess inventory and overproduction.
Perfection: Pursue perfection through continuous improvement. This principle emphasizes the importance of striving for zero defects and continuously seeking ways to improve processes, reduce waste, and enhance quality. It involves engaging all employees in the pursuit of operational excellence and innovation.
These principles together allow businesses to fully embrace the lean approach and help guide efforts toward greater productivity, efficiency, and customer satisfaction.
The Seven Common Wastes
Lean manufacturing also points out the seven common wastes found in industrial facilities, often called the “Seven Deadly Wastes”.
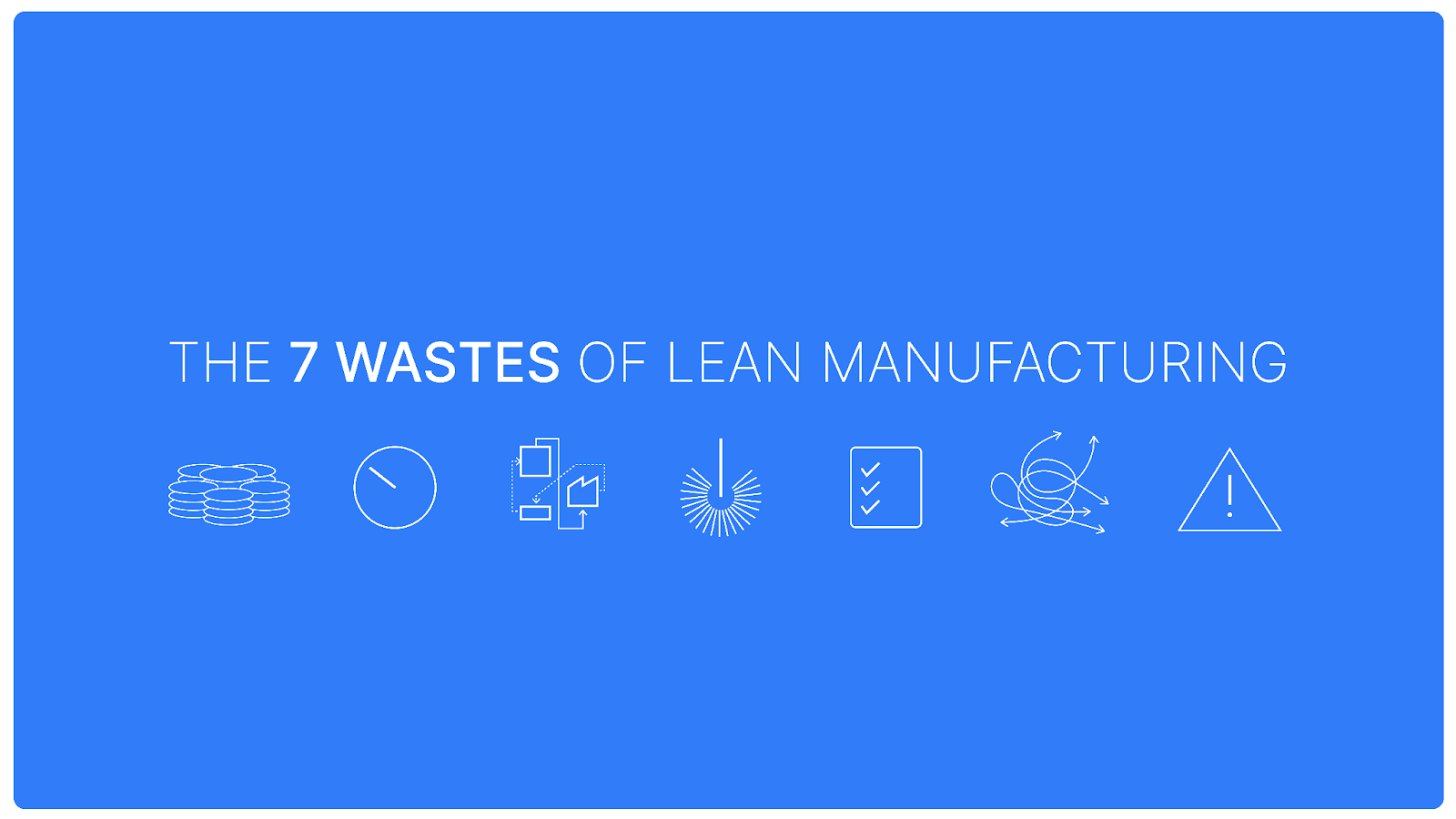
The 7 Wastes include:
Overproduction: Producing more than is needed or producing too soon. This leads to excess inventory and increased storage costs.
Delay: Any time that is spent waiting without adding value, such as waiting for materials, equipment, or information. This includes idle time of workers or machinery.
Transport: Unnecessary movement of products or materials between processes. This can lead to delays, potential damage, and increased handling costs.
Processing: Performing more work or using more materials than necessary. This can include rework, inspections, or any activity that does not add value from the customer's perspective.
Inventory: Excess products or materials not being processed. Excess inventory ties up capital, takes up space, and may lead to obsolescence or damage.
Motion: Unnecessary movements of people or equipment. This includes walking, reaching, or bending that does not add value to the product or process.
Defects: Producing defective products that require rework or scrapping. Defects result in wasted materials, time, and effort, and can lead to customer dissatisfaction.
Getting rid of these wastes is key in making production more streamlined.
The Benefits of Lean Manufacturing
Some of the greatest benefits as a result of Lean include:
Improved Efficiency and Reduced Waste: By streamlining processes and ensuring that only value-added activities are performed, companies can significantly improve their operational efficiency. This results in faster production times, reduced costs, and better resource utilization.
Enhanced Product Quality: Techniques such as Total Quality Management (TQM), root cause analysis, and standardized work practices help ensure that products meet high-quality standards consistently. As a result, companies experience fewer defects, lower rework rates, and higher customer satisfaction.
Increased Customer Satisfaction: By focusing on value from the customer's perspective and striving to deliver products that meet their needs precisely and promptly, lean manufacturing enhances customer satisfaction. The “pull system”, for example, ensures that production is based on actual customer demand, leading to faster delivery times and reduced lead times. Improved quality and reliability of products also contribute to a better customer experience.
Lean Case Study Results
A case study by the Lean Enterprise Institute reported that propulsion manufacturer Thrustmaster, achieved a 67% increase in on time delivery and reduced product costs to 100% or more of targets set over an 16 month period.
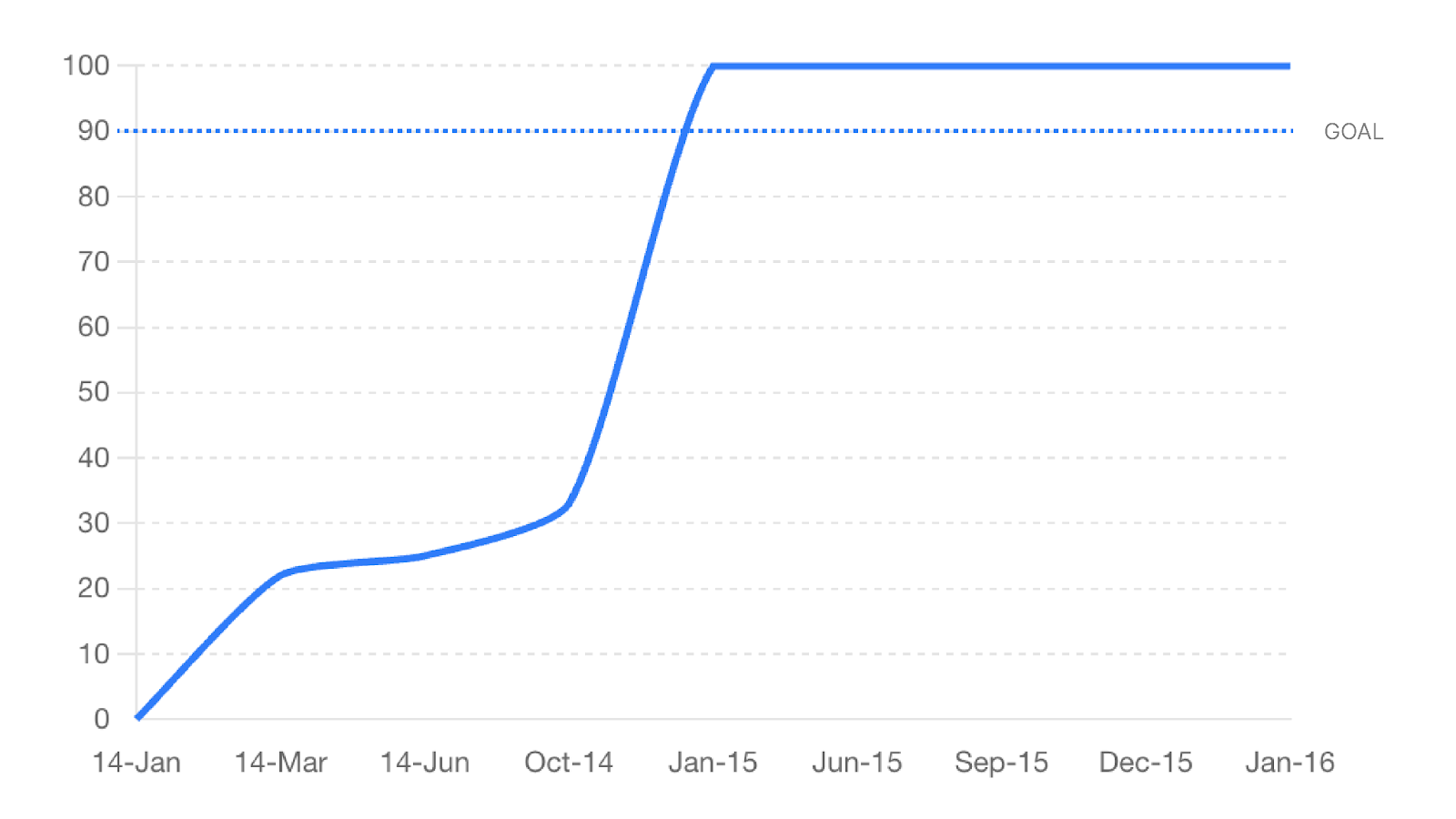
In their own studies, Boston Consulting Group found that on average, companies that successfully implemented lean manufacturing saw a 7% increase in sales, 10% decrease in production costs, and 6% reduction in inventory levels.
It's important to note that the actual impact of lean manufacturing initiatives can vary depending on factors such as the specific industry, the scope of implementation, and the organization's commitment to continuous improvement, but for most, going lean tends to have a very positive impact.
Lean Manufacturing vs. Six Sigma
A similar method that is often associated with Lean is Six Sigma.
While Lean manufacturing and Six Sigma both aim to improve processes, they focus on different areas. Lean focuses on cutting waste and boosting efficiency, whereas Six Sigma works towards better quality by reducing errors and variations in processes.
For many operations, Lean's approach offers more flexibility and encourages everyone to solve problems, fitting into companies with less hierarchy.
Lean Six Sigma combines both methodologies. It's a detailed, data-driven system that aims to cut down on many kinds of waste to create more customer value, manage resources well, and make quality better.
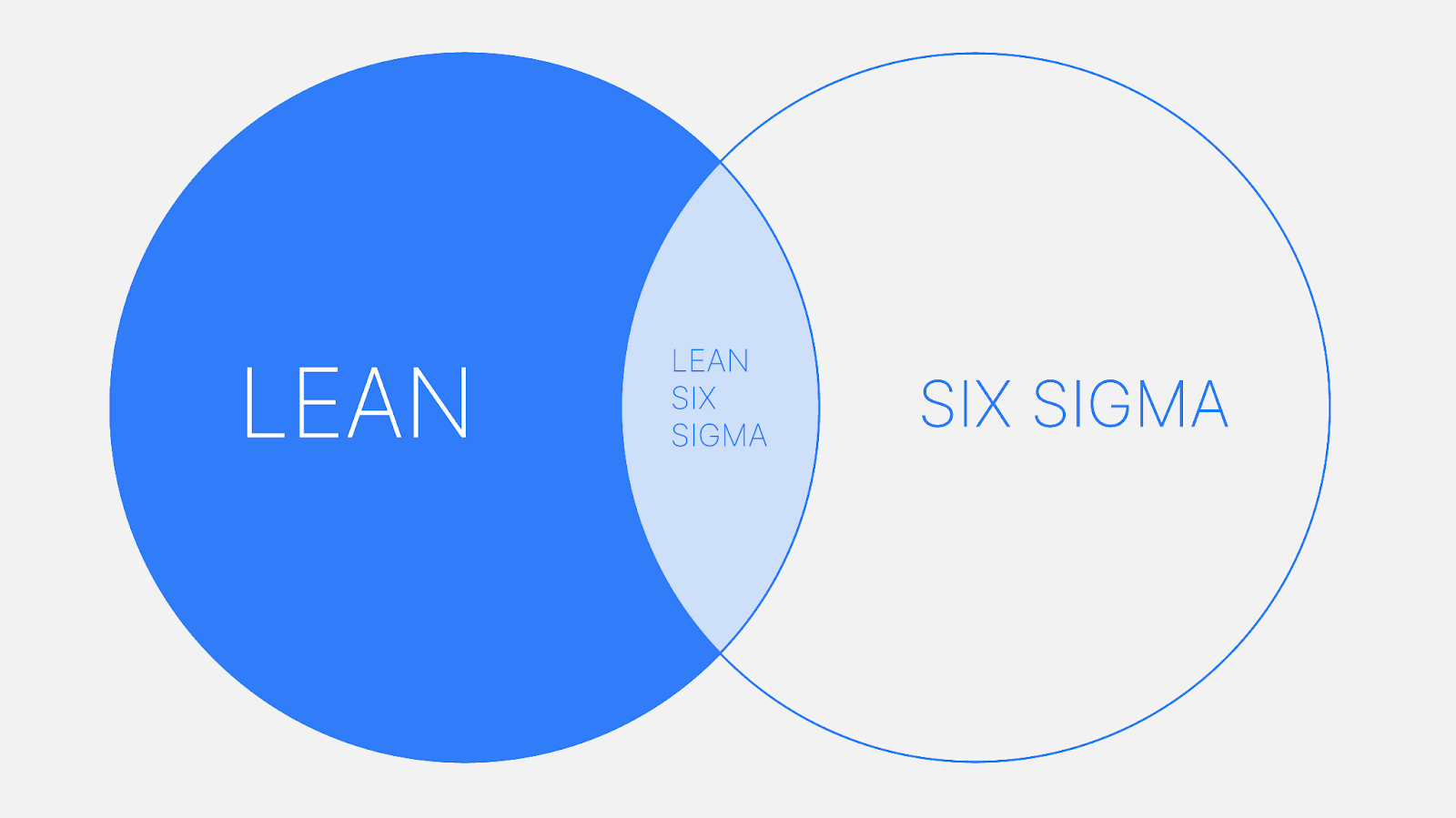
In Conclusion
Lean manufacturing, with its focus on value, value stream, flow, pull, and perfection, helps companies eliminate waste, improve efficiency, and enhance product quality.
These principles enable businesses to respond more effectively to customer demands, reduce costs, and create a culture of continuous improvement, ultimately leading to increased productivity, competitiveness, and profits.
Sources & Other Resources
For more detailed information on lean manufacturing and its principles, check out some similar articles and sources used below:
Toyota Production System
https://www.toyota-europe.com/about-us/toyota-vision-and-philosophy/toyota-production-system
The ROI of Lean Manufacturing
https://www.thefabricator.com/thefabricator/article/shopmanagement/the-roi-of-lean-manufacturing
TPS and Lean
https://www.allaboutlean.com/tps-and-lean/
What is Lean Manufacturing
https://www.twi-global.com/technical-knowledge/faqs/faq-what-is-lean-manufacturing
John Krafcik - Triumph of the Lean Production System
https://edisciplinas.usp.br/pluginfile.php/6889199/mod_resource/content/4/krafcik_TEXTO_INTEGRAL.pdf
Thrustmaster Case Study by Lean Enterprise Institute
https://www.lean.org/the-lean-post/articles/thrustmaster-comes-around/
Looking to implement LEAN into your facilities processes?
At LEAN Manufacturing Products we offer a wide variety of material handling and metal storage products that help optimize your project workflow and create a safer environment for your operators.