From Waste to Wonder: The Transformative Power of Lean Manufacturing
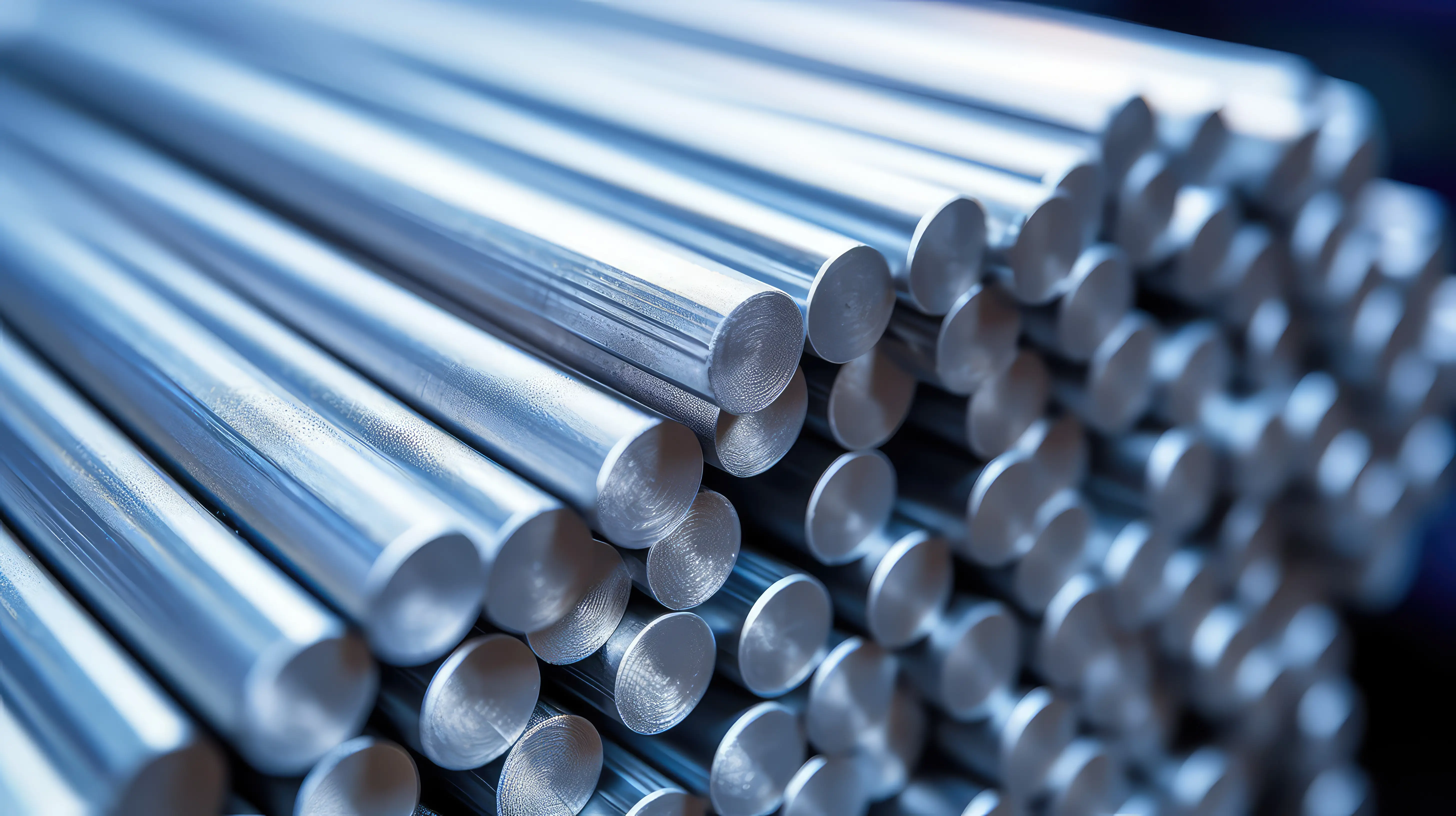
Achieving Business Success Through Operational Excellence
The incorporation of Lean principles into manufacturing operations has been shown to result in significant cost savings, streamed workflow, and increased efficiency.
This is achieved by identifying and eliminating non-value-added activities, such as unnecessary processes, transportation, and inventory, which can account for up to 90% of the total production time.
Implementing Lean enables organizations to improve product quality, as defects are identified and corrected earlier in the production process, reducing the need for costly rework and scrap.
In addition, organizations adopting the Lean philosophy promote a culture of perpetual improvement, encouraging employees to take ownership of their work and identify opportunities for growth.
The Future of Manufacturing is LEAN
By taking a comprehensive view of the entire manufacturing process, business owners can identify areas for improvement and implement lean principles to optimize your operation.
However, many manufacturers struggle to integrate the necessary products and solutions to support a lean process.
That's where we come in - LEAN Manufacturing Products is the leading provider of custom solutions to help manufacturers streamline their operations.
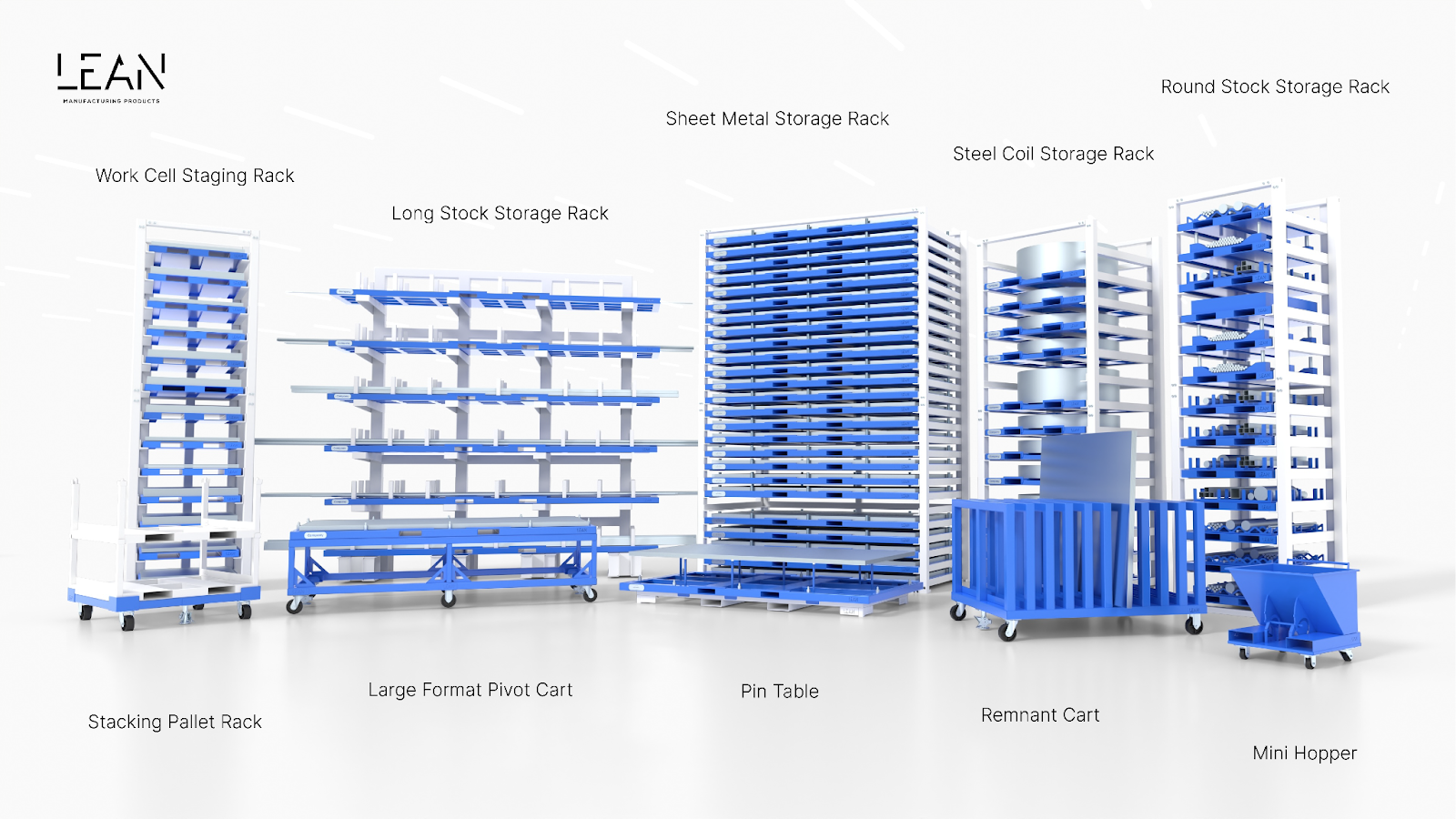
Our team has expertise in creating tailored solutions that integrate seamlessly with your existing processes, helping you achieve a more efficient and effective manufacturing process.
We have helped thousands of manufacturers all over the country identify their pain points and streamline their operations to propel their business to new heights.
From Reactive to Proactive: The Power of Lean in Manufacturing
Let's take a closer look at an example of the manufacturing operations for XYZ Sheet Metal, a fictional mid-sized sheet metal fabrication customer that has yet to implement Lean in their operations (based on real world customers).
Despite their best efforts, XYZ Sheet Metal has been operating in a reactive mode, prioritizing customer demand over operational efficiency.
Long lead times have become the norm, with orders taking an average of 6-8 weeks to fulfill. Inventory levels are excessive, tying up valuable warehouse space and significant capital investment. Furthermore, quality issues are frequent, resulting in a substantial amount of rework and scrap.
Employees often spend more time searching for materials and parts than actually processing sheet metal, leading to inefficient processes and low morale. The company's reliance on a reactive approach to production has also led to poor employee engagement, with workers lacking the autonomy to identify opportunities for improvement or make decisions that impact their work.
As a result, XYZ Sheet Metal is struggling to remain competitive in the market, with high costs and low productivity levels hindering their ability to respond quickly to changing customer demands.
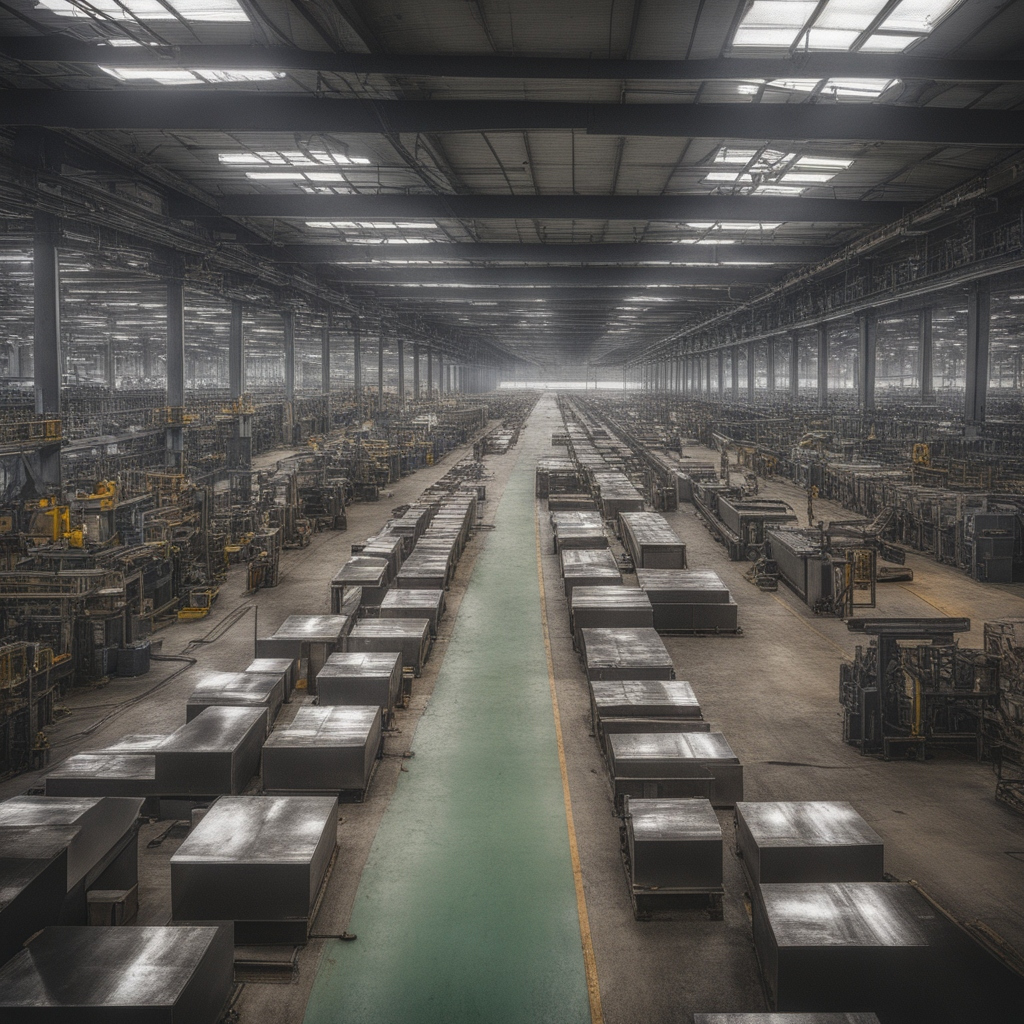
The Roadmap to Metal Processing Efficiency
To revitalize their operations, XYZ Sheet Metal reached out to LEAN Manufacturing Products and collaborated with our team to conduct a value stream mapping exercise to analyze their entire manufacturing process.
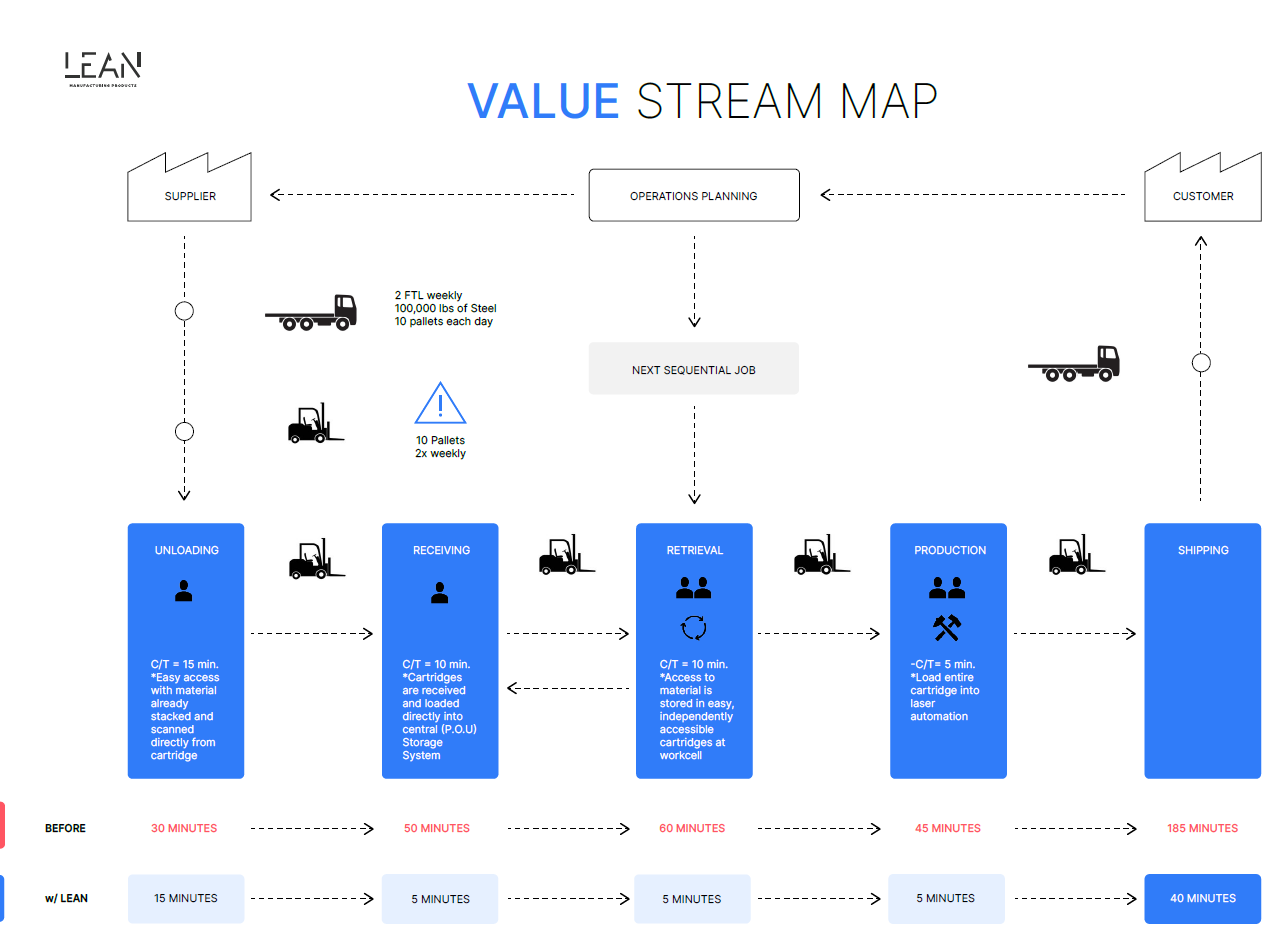
Through this exercise, XYZ Sheet Metal and LEAN identified several key areas where LEAN Manufacturing Products could be integrated to optimize current processes:
- Streamlining production workflows by integrating work-in-process staging racks to reduce lead times and improve responsiveness to customer demand
- Eliminating unnecessary inventory and optimizing material flow by incorporating LEAN pallet carts to minimize waste and reduce costs
- Implementing defect detection and prevention strategies to eliminate rework and scrap utilizing LEAN cartridges that safeguard material quality
- Empowering employees with the autonomy to identify and address bottlenecks and incorporating LEAN products to support their daily workflow
By targeting these critical areas, XYZ Sheet Metal aimed to create a more agile, efficient, and customer-centric manufacturing operation that would enable them to stay competitive in the market and drive long-term growth.
Lean Manufacturing Products: Where Efficiency Meets Profitability
After implementing Lean Manufacturing Products, XYZ Sheet Metal achieved the following results:
- Reduced lead times: Lead times were reduced by 50%, allowing customers to receive their orders faster.
- Inventory reduction: Inventory levels were reduced by 30%, freeing up valuable warehouse space and reducing capital investment.
- Quality improvement: Defects were reduced by 70%, resulting in less rework and scrap.
- Increased efficiency: Production line efficiency is improved by 25%, allowing workers to focus on processing sheet metal rather than searching for materials.
- Employee engagement: Employees are empowered to make decisions and identify opportunities for improvement, leading to increased morale and motivation.
Financial Benefits from Lean Manufacturing Solutions:
The implementation of Lean products to support XYZ Sheet Metal operations has resulted in significant financial benefits, including:
- Cost savings of $250,000 per year from reduced inventory levels
- Cost savings of $150,000 per year from reduced waste and rework
- Increased revenue from faster lead times and improved quality
- Improved customer satisfaction, leading to increased loyalty and retention
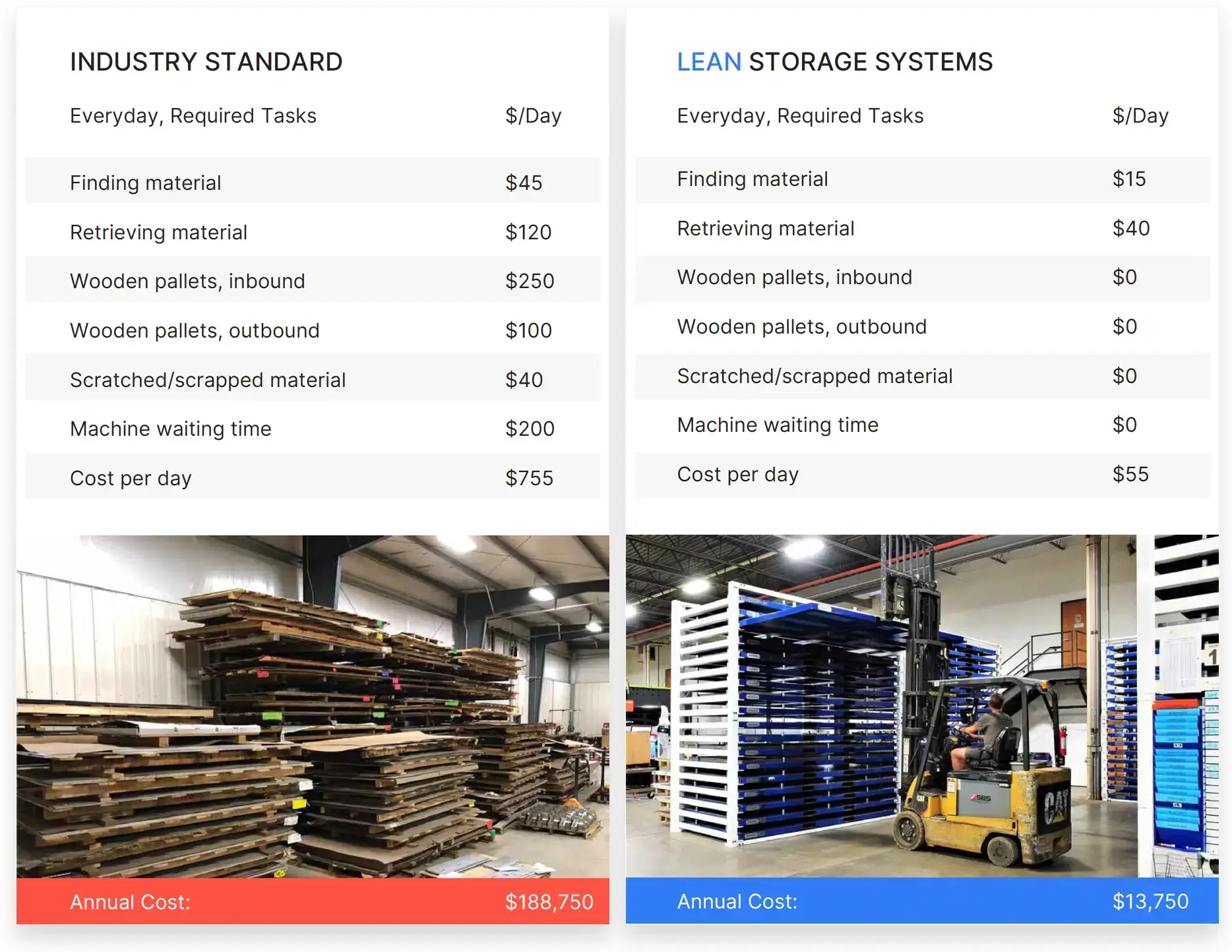
Through the successful implementation of Lean Manufacturing Products, XYZ Sheet Metal has undergone a profound transformation, revolutionized their operations and propelled themselves towards a new era of competitiveness.
By eliminating waste, optimizing workflows, and empowering employees, the company has become a more agile and responsive organization, better equipped to adapt to changing market demands and customer needs.
Transform your operation
Looking to improve on your own facility processes?
Our team will work closely with you to analyze your current process, identify areas for improvement, and implement tailored solutions to drive business growth.
To view our full offering of Top-of-the-line material handling and metal storage products, visit the product page here.
Have questions? Give us a call at 262-875-3071 or shoot us an email at info@leanmfgproducts.com